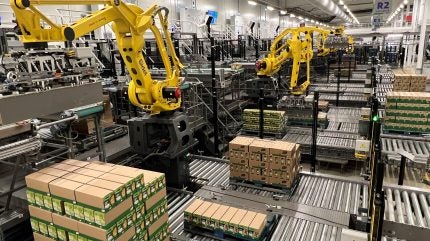
Manufacturing company Sidel has supplied FMCG (fast-moving consumer goods) leader Unilever with a palletising system for its nutrition factory in Ploieşti, Romania.
The system contains eight robotic cells, several hundred metres of case and pallet conveyors, four pallet handling shuttles and two stretch wrappers, achieving a production rate of up to 98 pallets an hour. The consolidated system is connected to 28 packing lines.
The factory manufactures products for one of Unilever’s most well-known brands, Knorr. The dry nutrition portfolio includes a range of packaging formats – pouches, bags, cartons and multipacks.
The product lines also handle a large variety of secondary packaging options – American boxes, tray and hood, tray and shrinking foil, and shelf-ready packaging.
Sidel’s robotic cells are divided into two separate clusters – one with five robots, and the other with three. Each cluster has one central magazine for all pallet types and sizes, one induction shuttle for full pallet discharge and one compact shuttle for empty pallet delivery integrated underneath the robotic islands.
According to the capacity of each packing line and the palletising pattern requested, the cells have three or four product in-feeds, ensuring a robot utilisation rate of 92%.
Unilever’s masterplan for the Ploiesti site was to keep the pallet space in a separate area from the packing hall to easily accommodate recurring packing line modifications. To connect the two areas, Sidel proposed a conveying solution with spiral elevators to save space, facilitate circulation and increase the overall flexibility linked to site transformations.
The central palletising system is integrated into the Unilever digital process. Once the operator selects the production order from the packing line, all the information related to the palletisation – including pallet size, type of pattern, number of rows or layers and the label to apply – is all automatically set and transmitted to the corresponding palletising cell and the entire end-of-line setup.
Sidel recently joined forces with sustainability assessment company EcoVadis to drive its sustainable supply chain initiatives.