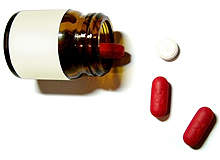
Mistakes happen. Some – forgetting your keys for instance – are little more than a trifling annoyance. Others, like misreading the label on a medicine bottle, can be fatal. And if it’s the manufacturer that makes a mistake, and incorrectly labels a whole batch of medicine bottles, the result could be catastrophic.
To avoid this doomsday scenario, new regulations covering how packaging companies produce labels are being drafted. From smudging to clarity, the emphasis will be on getting the packaging and labelling right.
So what is the right label?
Medica Packaging, formed in the 1920s but part of the Benson Group since 2005, is a major manufacturer of medical packaging and patient information leaflets. The size and fonts used on the labels are governed by regulations, and the artwork is supplied as a PDF from the pharmaceutical company. Medica’s job is to ensure the quality of the printing is consistent in each batch. Along with security, its main aims are to maintain clarity, legibility and consistency of print.
It is essential, says Andy Riggs, Medica’s business manager for labels, to make sure that there are no rogue labels in the reels and that printing plates are specific for each label.
Reels are printed in rows using a web printing process, where each row is printed at the same time. For example, row one could assigned to 5mg of aspirin, row two to 10mg aspirin, row three 15mg and so on.
"Doing it this way saves money but can cause problems," Riggs says. "When you splice reels together, you may accidentally link two different reels and end up with the wrong label. The answer is to not gang print like this but to cut them into single reels."
All is not lost even if a mistake is made at this stage: the labels are later checked by system that can detect if the wrong barcode has been used or if there is a problem with print quality.
"The printing plates have to be robust enough to make sure that the quality of the print doesn’t deteriorate during the run," says Riggs, who adds that even small blemishes or patches of missing print can have dire consequences.
"If the full stop in '1.5mg' doesn’t print it can look like '15mg', so you need a robust system to ensure that doesn’t happen."
Medica does this through a combination of human checks and a computerised visual inspection system. For extra security, a protective coat of varnish can be applied. In some cases, polyethylene labels are used – these have a treated surface that stops the ink rubbing off.
"Ten to 20 years ago, we used to get a lot of problems with smudged text. Labels rubbed against each other and that could scratch the print. That very rarely happens now, and we have checks in place to catch it if it does," says Riggs.
Changing labelling standards
Companies such as Medica have had to take on more responsibility for medical labelling in recent times, according to Riggs, with pharmaceutical companies expecting label suppliers to make sure that there are no problems.
Printers such as Medica must follow the rules of the Pharmaceutical Quality Group (PQG), which stipulates the key quality standard in this area – PS 9000. This sits alongside other general quality standards such as ISO 9000 and ISO 9008.
PS 9000 covers pharmaceutical packaging that is not in direct contact with medicines, and labels on bottles and cartons. It was produced in 2000, but a new version is being drafted and is expected to be ready early in 2011. The PQG committee working on this new draft is chaired by David Abraham of packaging firm Firstan.
"We are updating the requirements for supplying the pharmaceutical industry to improve security and confidence," he says. "We are covering cartons, leaflets and labels."
The standard went through a major upgrade shortly after its inception, expanded from just over 50 pages to almost 200, to cover all aspects of the process, right through to the end customer. But changes in security technology mean that it is now out of date.
The updated version, Abraham says, will include new security features and change control – how to manage when, for example, a new piece of equipment has been installed. Areas such as counterfeit prevention, barcoding and dot matrix codes will also be covered, as will the need for quirky designs on labels that are hard to copy.
"We are also looking at inks and varnishes," he says. "This will include invisible ink that can be read only in ultraviolet light, and we are looking at applying a composite as part of the label material to identify it as a legitimate product."
October 2010 heralds another change: Braille information will need to be included on all new products. This, followed by the updated PS 9000 standard in early 2011, means that companies such as Medica will have their work cut out for them in the coming months.