Flexible pouches are here to stay. The number of manufacturers adopting this method to package their products grows daily. A wide variety of products are now packaged in this high-tech manner, including detergents, dried fruit, coffee, yoghurt, pet food, soft drinks and soups. So what advantages does this container method have that can explain its success?
Versatility is the key. With modern lamination and polymer co-extrusion, hybrid materials with a range of desirable properties (such as strength, a polished finish and barrier integrity) can be produced. These properties can be tailored into a flexible pouch containing a variety of products, ranging from liquids to semi-solids and dry solids.
Flexible packaging can incorporate a range of closures, including spouts, zip lock closures and tape closures. Flexible pouches protect products more efficiently than cans, glass and cardboard, and are increasingly more convenient for the consumer. Their flexible nature also makes them easier to stack and store, which is beneficial to both supermarkets and transporters.
Laminate layers
Flexible pouches can combine a multitude of layers in their laminated structure. These may include various polymers, such as polyethylene, nylon, polypropylene, polyethylene terephthalate, EVOH, aluminium foil, silicon dioxide, and ceramics.
Each layer has a function and a property to impart to the pouch. The combination of these layers in a ‘recipe’, or formulation, makes up the laminate from which the pouch is constructed. The laminate produced depends entirely on the final intended use. For example, some pouches are designed to be heated in microwave ovens as a disposable bowl, and cannot have a foil layer in the laminate: they are constructed with a heat-resistant laminate instead.
Alternatively, coffee packaging needs to have very good barrier properties to seal in flavour and prevent moisture entering. In this case, the barrier properties and strength of aluminium foil are used in conjunction with EVOH resin.
How well do you really know your competitors?
Access the most comprehensive Company Profiles on the market, powered by GlobalData. Save hours of research. Gain competitive edge.
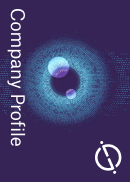
Thank you!
Your download email will arrive shortly
Not ready to buy yet? Download a free sample
We are confident about the unique quality of our Company Profiles. However, we want you to make the most beneficial decision for your business, so we offer a free sample that you can download by submitting the below form
By GlobalDataThe use of flexible pouches in the drinks packaging industry has been restricted to ‘still’ products. However, their versatility will extend further as laminates are developed with sufficient barrier properties to contain carbonated drinks. Despite technological advances, it is unlikely that flexible pouches will ever make an impression on the carbonated drinks market, as PET bottles and aluminium cans are too well established.
Factors of success
The success or failure of a packaging system relies on a number of factors:
- Efficiency of the container
- Impact of graphics
- Cost of the system
- Ability to seal/reseal the utility
- Range of purpose
- Recyclability
Flexible pouches have satisfied all of these criteria. The basis for the success of this container method must start with the resin and film suppliers (dedicated to developing materials that meet barrier requirements), the converters (for the design and construction of the packaging) and finally the packaging end-user (for having the vision to use a new packaging system).
One of the most prominent companies in the flexible pouch field is Amcor Flexibles. It provides a range of technological services, including state-of-the-art gravure and flexo printing, coating and lamination, co-extrusion, metallising, micro-perforation, and pouch and bag making.
The latest innovation from Amcor is Forge, a short-run print process service (15,000m2) for packaging design and development. The packaging solutions available in the flexible pouch area include high-barrier transparent materials, laminated metallised films and a range of easy-open and closure options, including tear tops, TapeTop and zip-lock closure. The Amcor flexible pouch range includes:
- EasyPack: A stand-up pouch that can be easily opened via a tear strip and closed using a zip-lock closure system.
- FlexCan: A new stand-up flexible container that is simple to open, pour from and reclose. This is produced for the fresh juice and still beverage markets.
- HeatFlex: A flexible pouch that uses multilayer transparent or foil-based laminates, which are specially designed for retort treatment and suitable for microwave heating.
- P-Plus: A flexible pouch range that uses tailored-permeability films for modified atmosphere packaging, which is designed to maintain freshness and extend the shelf life of fresh produce.
Cracking the code
Amcor TapeTop is a new design that allows a reclosing mechanism to be incorporated into flexible pouch design. The packaging machine uses a small strip of the extra material to form a reclosure tape. The reclosure tape is coated with a hot-melt adhesive and is positioned on the pouch surface using ‘cut and transfer’ technology. The use of hot-melt adhesive is more expensive, but it ensures that the closure can be used with virtually any material surface.
The system is suitable for a wide range of products, from frozen foods to coffee, detergents and snacks. Jonathan Fowle, business development director of Amcor Flexibles, says, ‘The key to the success of Amcor TapeTop is that we supply it as an integral part of the laminate.’
Serial coding is a unique system that can print an individual message or number in ASCII characters on separate pouches. The process can be carried out simply using computer-controlled inkjet printing, in line with a gravure press. The system is ideal for tracing products, as each package has a unique code or number that allows it to be identified.
This helps producers to counteract counterfeiting and retailers to monitor shelf life dates. It can also be used for promotions and games. Fowle adds, ‘The unique coding number can potentially be put on every wrapper you see.’
Battenfeld Gloucester Engineering (BGE) is a major supplier of extrusion equipment for the fabrication of blown and cast film, and thin sheet-foam for thermoforming. It supplies a wide range of machines to satisfy customer requirements. German Laverde, director of marketing and communications at BGE, says, ‘We allocate resources to give customers a variety of tools to help them produce films for the converting process. BGE offers improved air-ring designs for the blown film process, allowing better bubble control, higher output and less variation in thickness.’
BGE sees the future of flexible pouches as, ‘replacing rigid containers and offering more convenience to the consumer.’ According to Laverde, the important advances in flexible pouches will be, ‘co-extruded film structures, allowing an extended shelf life, along with enhancements to graphics and printing technologies and innovations in valves and fittings’.
Barrier resin
EVAL Europe, a subsidiary of Kuraray Co Ltd in Japan, is a leading producer of ethylene vinyl alcohol (EVOH) resin – an important component of flexible pouches. An expansion at the Antwerp plant in Belgium, due to be opened in late 2004, will make it the largest EVOH production plant in the world, with an annual production capacity of 24,000 tons per year. The EVAL EVOH resins can be supplied as pellets for use in all standard co-extrusion equipment (including the production of cast and blown film), or alternatively as speciality monolayer films for lamination processes. EVOH is known for its superior barrier properties. Its ‘7 series’ of polymer grades have superior thermal stability.
However, in order to achieve specific forming or orientation properties on secondary processing, it has sometimes been necessary to increase the ethylene content of the polymer. William Reay, sales and marketing director of EVAL Europe, explains the process, ‘Using an EVOH grade with high ethylene content sacrifices some of the barrier properties. However, a new product line, the ‘SP’ series of orientable EVAL, will be launched in late 2004. It will offer superior barrier properties and excellent secondary processing. The company is now concentrating on secondary processing to allow customers to form deeper, orient wider and sterilise under increasingly severe conditions.’
EVAL Europe expects that the application of EVAL EVOH resin will widen to compete as a chlorine-free option in PVDC applications. When it is released on the market, the new ‘SP’ orientable EVAL will be one of the most advanced EVOH resins available.
Flexible film
Manuli Film SpA is an Italian company that specialises in the production and supply of bioriented polypropylene (BOPP) film to the packaging industry. It manufactures and markets the Manucor range of BOPP films. BOPP is an extremely versatile material; as well as being an important component of flexible pouches, it has recently been adopted for PET bottle labelling in the beverages industry to aid the recycling of bottles, where paper labels were difficult to recycle with PET bottles.
Manuli has recently developed a new metallised film for flexible pouch manufacture. Alessandro Rolla, marketing and sales manager at Manuli, explains the strategy behind the new product. ‘Our job is to persuade customers that the new Sealable High Barrier Metallised film from Manuli will perform as well as existing films, but at a fraction of the cost. The applications we are considering are for food: particularly food with aromas that must be sealed into the packaging.’
Most of us have seen flexible pouches in our supermarkets. The increased sales figures of these products, with their larger, more noticeable graphics (achieving point-of-sale differentiation), support the popularity of this container method. Could we be on the brink of a packaging revolution? Recent innovations in development and strong consumer support would suggest that we are.