Change is the only constant in the packaging market. As the variety of food packaging increases, developers of films and coatings must try to stay ahead of their clients’ demands.
Packaging produced today needs to address the issues of tomorrow, while helping converters and end users to manage their costs. Observing trends in customer requirements and anticipating market developments is key to the development of any company that wants to open up new markets.
DuPont Teijin Films (DTF) has its eyes fixed firmly on the future. DTF is one of the world’s leading suppliers of PET and PEN polyester films. Their broad portfolio of Mylar polyester films for packaging excels in many market areas including freshness, on-shelf impact and convenience.
Among the firm’s breakthroughs is a hygienic meat packaging and cooking solution that improves presentation, convenience and taste, as well as extending the meat’s shelf life, so reducing waste. The ovenable laminate joins a barrier layer, that provides freshness protection meeting the 12-day shelf life requirements, while the heat-seal layer is fundamental to pack formation.
As the leading European supplier of polyester films, DTF also works in some niche areas such as shrink-sleeve packaging. ‘We developed shrink-sleeve capability some years ago,’ says Dr Gary Rhoades of DTF. ‘The shrink-sleeve market in Europe was dominated by PVC, and the move towards polyester film shrink solutions has been primarily driven by growing environmental concerns. We are the only European polyester film manufacturer to include shrink-films in our portfolio.’
Converter partners
‘It is an attractive and growing market,’ says Rhoades, ‘and we are continually striving for innovation. Recently, our development partner Hewlett-Packard showed a new concept film suitable for digital printing. This film enables shrink-sleeves to be printed quickly on short runs.’ Smaller printers could produce novelty products. DTF expects more serious applications to develop, as digital printers become more prevalent and issues such as traceability more important.
How well do you really know your competitors?
Access the most comprehensive Company Profiles on the market, powered by GlobalData. Save hours of research. Gain competitive edge.
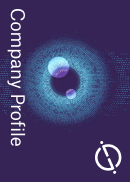
Thank you!
Your download email will arrive shortly
Not ready to buy yet? Download a free sample
We are confident about the unique quality of our Company Profiles. However, we want you to make the most beneficial decision for your business, so we offer a free sample that you can download by submitting the below form
By GlobalData‘It is important for us to offer flexibility. We have a close relationship with HP, and spend a lot of time working with the entire value chain.’ Printing firms are able to combine old and new technologies by printing labels with the company livery using litho or gravure, and then adding ‘just-in-time’ elements using digital technology.
‘At the moment this is a concept film, but DTF’s capability to manufacture it will be important as the market starts to react to new technology. We must keep showing innovation and responsiveness in the development of polyester films, and speed up the time between concept and product. We want to continue to work with our customers in niche areas that are consistent with our overall strategy.’
Specific solutions
Along with advances in films, there have also been innovations in coatings for packaging materials. ‘What we deal with is 90 per cent coatings for paper- and board-based packaging,’ says Niko Kinnunen of Clariant. ‘We look at how to treat each product, and then make the packaging suitable for the specific purposes of end users. We are mainly concentrating on the growth areas, which are grease and moisture resistance. We tend to work with technologies that are not already established.’
Polyethylene extrusion (PE) coating is well known, but Clariant has been exploring an alternative water-based chemistry. With PE coatings, customers might end up with a product that exceeds their requirements in terms of material properties. Clariant believes that designing water-based solutions for specific uses – such as grease resistance for fast food packaging – will improve efficiency and reduce costs.
Cost is the major driver of development in the packaging industry. Margins have become tighter, so cost-effective solutions are welcomed. ‘Our technology has been in development for a long time, just as PE technology was before commercialiation,’ says Kinnunen, ‘and I would say that it is easily adaptable, but can still be optimised.’
Contact coatings
Clariant has seen a lot of interest in its Cartaseal FTU and VGL liquids, as well as its Cartafluor range. Cartaseal FTU liquid is a product that imparts resistance to paper or board against water, oils, fats, grease and solvents. The liquid forms a flexible film, even over folds and creases, and is used in the packaging of pet foods, fast food and confectionery, where the status of food contact is essential.
Cartaseal VGL liquid acts in a similar way to the FTU liquid, but it has been designed to include a water vapour barrier. It is used to make various types of food packaging paper; an area where contact is a key consideration. The Cartafluor range is slightly different, in that it is based on fluoro-chemicals, but provides grease resistance that makes it ideal for pet food packaging.
At the moment, Clariant is making a concerted effort to bring water-based coatings to the market. ‘As with anything new, a degree of confidence and familiarity needs to be built,’ observes Kinnunen.
‘There is competition from existing technology, but when we started to research our technology the cost base was different. It is now more favourable. The initial cost may be greater, but the long-term savings might be more significant. There are also further benefits to be had from water-based technologies: the products are recyclable, and the coating does not require the separation process that PE or wax-based coatings need. It can be re-pulped with the fibre and board.’
On the shelf
While working on bringing its existing products to the wider market, and extending their use, Clariant is also working on the development of a water-based oxygen barrier for food that requires a longer shelf life.
By pooling technological advances in the development of coatings and films for a variety of products, packaging manufacturers will soon be able to offer comprehensive protection and impeccable print quality to their clients.