
Germany-based KHS has developed a new crowner that will help to maintain hygiene standards in beer filling systems.
The crowner has been tried and tested for microbial safety, and helps to reduce cleaning times.
The design and dimensions of the new crowner have enabled bottlers to retrofit the new product into their current lines.
KHS plans to include the newly developed crowner in its future beer filling systems.
KHS filling product manager Manfred Härtel said: "The crowner is a critical element as it constantly has to operate in beer residue.
“This is a challenge during operation which we've been able to considerably improve and alleviate."
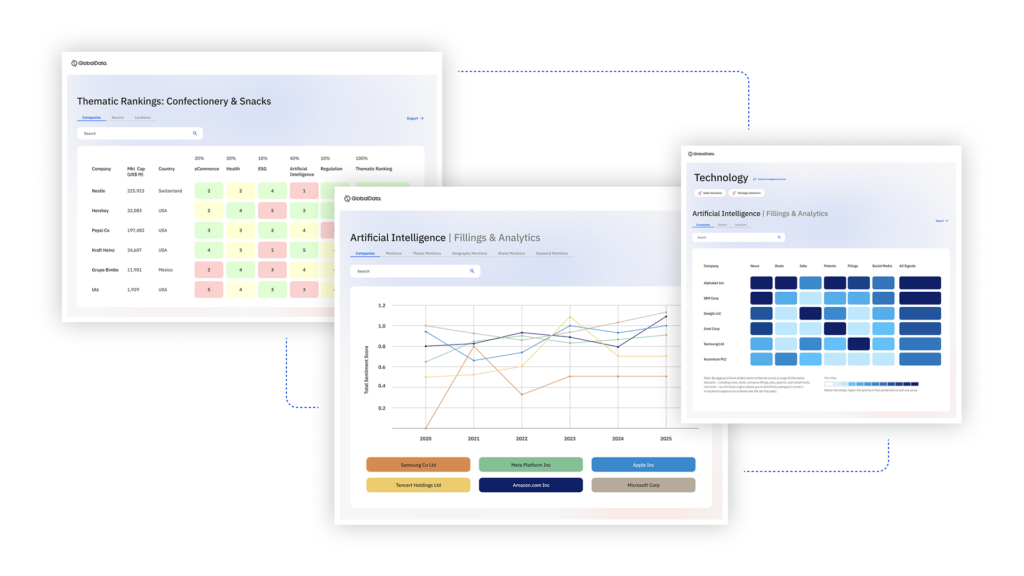
US Tariffs are shifting - will you react or anticipate?
Don’t let policy changes catch you off guard. Stay proactive with real-time data and expert analysis.
By GlobalDataThe new design provides more forceful rinsing and reduces the amount of residual beer left on the components.
To improve hygiene, the contact area from the head piece to the capping ring of the new crowner has been reduced.
KHS has increased the distance between the crowner's cork shoe and head piece to allow optimum flushing.
A special sealing ring has been added to check beer flowing into the thread of the crowner.
Two more flushing openings have also been included so that the rinsing element can easily access the soiled areas inside the machine.
In addition to craft and draft beers, non-alcoholic beers can also use the new crowner.
During the beer filling process, oxygen must be prevented from entering the inside of the container when bottles are closed.
Contact with oxygen reduces the beer's shelf life and causes it to develop an aging taste.
The crowner should stay microbiologically clean during closure so that it does not contaminate the beer bottles.
Image: The new KHS crowner increases microbial safety during beer filling and shortens cleaning times. Photo: courtesy of KHS.