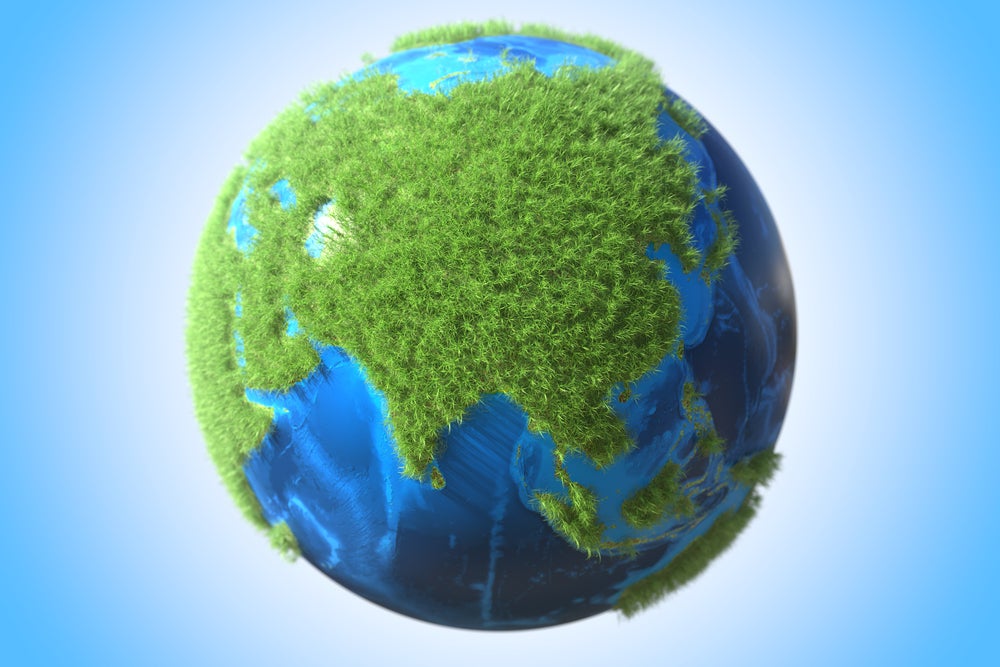
To find a model of integrating sustainable packaging into people’s everyday lives, packaging industry figures need look no further than Asia for shining examples of what is possible.
According to GlobalData, the continent is set to lead the global polyethylene terephthalate industry capacity additions with a share of 61.8% by 2027, a crucial material in sustainable packaging.
On the level of individual companies in Asia, major progress is being made in the manufacturing of sustainable packaging materials.
Recently, ALPLA Group and PTT Global Chemical achieved a milestone with the launch of the first food-grade recycled polyethylene terephthalate (rPET) bottles in Thailand. Meanwhile, ALBA Group partnered with VietCycle to develop a plastic recycling facility in Vietnam.
These are only a snapshot of some of the exciting sustainable projects happening across Asia.
To uncover how to scale such sustainable packaging initiatives in Asia, Packaging Gateway interviews Nicole Rycroft, founder and executive director of environmental non-profit Canopy.
Which countries in Asia have the most impressive track records for sustainable packaging?
Countries like Vietnam and Thailand have recently made headlines by replacing plastic packaging in supermarkets with biodegradable packaging such as banana leaves.
Meanwhile, China and India boast 75% of current global agricultural residue pulp-paper-packaging production – with many of the older, dirtier technologies having been closed.
This experience strongly positions India and China within the next 3-5 years at the forefront of sustainable packaging production – which will also help reduce their reliance on imported carbon-intensive wood fiber.
Why is Asia well-positioned to be a leader in sustainable packaging?
Asia is a manufacturing hub for much of the world’s consumer goods and clothing, from clothing to cell phones. Given that products are generally packaged on-site, it positions countries like China, India, Indonesia, Vietnam, and Bangladesh to become leaders in low-carbon next-generation packaging production.
The continent’s experience in working with natural materials such as straw, used as a feedstock for pulp production, along with the region’s documented abundance of raw materials, such as agricultural residues and food waste, makes it a prime candidate to be an early global production hub of low-impact packaging. Making packaging from straw carries, on average, four tonnes less carbon per tonne of packaging, has five times less impact on biodiversity, and requires 70 – 90% less water for production than a wood-based packaging product.
What are the challenges of turning agricultural waste into packaging?
Pulp and packaging mills are big-ticket infrastructure investments, so building the production capacity for clean straw packaging requires significant capital investment.
We estimate that over the next decade, $78bn will need to be mobilized into the next-generation pulp, packaging and viscose textile sectors – to turn excess volumes of agricultural residue that are currently burned in the field into low-carbon packaging.
Global pulp, paper and packaging is currently dominated by virgin wood production. This “take, make, waste” production system has become entrenched over the past 150 years. We need to retrofit at least a third of the existing commercial infrastructure by 2033 to switch to more sustainable alternatives.
This will also require training and familiarisation for pulp engineers who have primarily worked to date with wood so they become equally skilled and dexterous in working with agri-wastes.
The industrial ecosystem around individual pulp mills – the systems for the aggregation and pre-processing of agricultural wastes, working with farmers to ensure they provide the quality required – also needs further development. Given that Asia already has a vibrant straw pulping sector, it has an advantage on many other parts of the world. But there still needs to be further development and refinement to scale.
None of these challenges are insurmountable and can be significantly helped by:
- National and regional governments establishing programs that create enabling conditions – be it establishing regional training programs for farmers, tax incentives for conventional producers to retrofit their existing facilities, or favourable permitting for new next-gen tech to build mills regionally.
- Global and regional brands step forward to purchase from next-gen producers early to market. Our experience is that the clearer the market signals are for the supply chain that they need to adapt, invest, and switch to more sustainable practices, the faster the transition happens.
There may be current gaps in the system, but change can happen quickly and we expect the switch to bring significant economic, social, and environmental benefits to Asian countries that are at the forefront of this transition.
Using discarded textiles and agricultural residues to make packaging rather than trees will alleviate the pressure off forests worldwide so that irreplaceable rainforests like Indonesia’s Leuser Ecosystem can be protected and the peatlands in Indonesia can be restored. It also presents a significant opportunity for farmers to earn value-added revenue for currently a waste management issue.