The circular economy aims to minimise health-injurious waste and maximise sustainable resources by re-capturing the base materials from “waste,” and repurposing them to create climate-improved products.
Recycling plays a crucial role in closing the loop and reducing our dependence on virgin resources. Traditional mechanical recycling has long been used to process various waste materials, but it has significant limitations. Chemical recycling can enhance the near-term possibilities by delivering “new” raw materials that can be used to create sustainable products and strengthen the circular economy throughout the world.
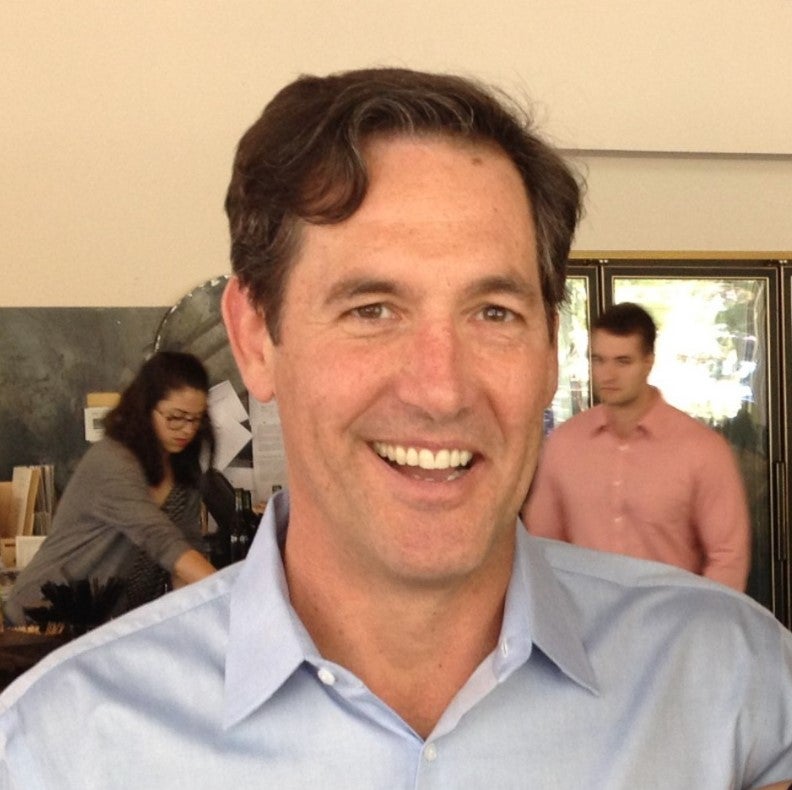
Pyrolysis is a chemical recycling method in which waste materials are thermally decomposed without oxygen. By heating plastics under controlled conditions, liquid hydrocarbons, carbon black, and gases are produced. Using these end products as feedstocks for the production of new plastics or other materials would not only help climate improvement but would also reduce our dependence on virgin fossil fuels and virgin resources.
There are limitations to mechanical recycling since it can only process waste streams that are clean and homogeneous as well as sorted into very specific categories. The recycling of contaminated, mixed, or degraded materials often results in lower-quality products or is simply diverted to local methane-emitting landfills. Mechanically recycled materials may also lose quality after multiple recycling cycles, as mechanical processes can cause physical and chemical degradation.
By contrast, chemical recycling can handle more complex waste streams because it breaks down materials at the molecular level, which allows it to recycle a wider range of materials. Pyrolysis, for example, can overcome this problem by producing high-quality end products that can be used for making new products without compromising their properties. Pyrolysis technology is now successfully used to transform mixed plastics (except for PET, which is typically mechanically recycled, and PVC). Chemical recycling output quality is impacted by the materials used in the process since input materials are converted back to their base raw materials.
Furthermore, there is a breakthrough system for processing mixed plastics, including PVC plastics, that removes chlorine prior to entering the pyrolysis chamber, which is great news for waste streams containing substantial PVC plastics.
The pyrolysis process can also reduce greenhouse gas emissions by replacing virgin fossil fuel feedstocks with recycled ones. Additionally, the pyrolysis process itself can be energy efficient since it generates gases that can be captured and used for heating or electricity generation. As a result, the carbon footprint of the recycling process can be reduced, supporting the transition to a low-carbon economy.
There are some types of plastics that are difficult to recycle through traditional mechanical methods, such as multilayer packaging and contaminated materials. It is possible to divert these hard-to-recycle waste streams from landfills and incinerators through chemical recycling. As a result, not only is waste reduced, but valuable resources are also preserved. By creating healthy and valuable end products through chemical recycling technologies like pyrolysis, new market opportunities can be opened up. Chemicals, construction, and transportation industries can use these materials as feedstocks. As a result, new economic opportunities and jobs can be created in the recycling industry as well as new product design and material usage innovations.
Chemical recycling
While chemical recycling offers numerous benefits, it is equally important to acknowledge the challenges and considerations associated with its implementation. These include the upfront investment and operational costs of chemical recycling facilities, which can be significant, as well as the quality of output recycled raw materials – and their market prices. The quality of raw materials for end-of-life tires (“EOLT”) plays a significant role in the economic viability of the product. Chemical recycling of EOLT produces recycled carbon-black (“rCB”) and pyrolytic oil, both of which can be used for tire, plastics, chemical and paint manufacturing. Also important, high-quality rCB (N330 and above) will sell for US$1000-$1500 per ton, while low-quality rCB will sell for US$100-200 per ton.
There have been significant advancements in the technology of chemical recycling pyrolysis facilities in recent years, including lower facility costs, more efficient and longer-lasting operations, and smaller plants. Decentralised transformation of waste is now feasible in markets worldwide, with plastics and tire conversion plants providing profitable outputs for facilities as small as 15 tons/day for plastics and 35 tons/day for EOLT. Humans create waste where they live, and when waste streams can be processed near the collection point, with pyrolysis the carbon footprint can be significantly reduced.
It is important to evaluate the energy and resource efficiency of chemical recycling processes, considering factors such as energy consumption, water consumption, and environmental impacts. Through the optimisation of these processes and the integration of renewable energy sources, chemical recycling facilities can reduce their environmental footprint. In the best chemical recycling systems, more than 60% (ideally 80%) of the raw materials can be recycled, and the plants can generate their own heat and electricity.
Aside from pyrolysis, there are other chemical recycling processes that support the circular economy. Waste materials can be broken down into valuable material products through these processes which contribute to sustainability goals. Some of these processes include: i) solvolysis – a chemical recycling method that uses solvents to break down waste materials into their constituent monomers or oligomers; ii) depolymerization – a process that breaks down polymer chains into their constituent monomers; iii) hydrolysis – a chemical recycling process that involves breaking down waste materials using water, often in the presence of catalysts, acids, or bases and iv) enzymatic – using enzymes, which are biological catalysts, to break down waste materials, into their constituent monomers or oligomers.
Maximising resource efficiency and minimising environmental impacts requires a holistic approach that considers waste reduction, reuse, and recycling. To develop effective strategies for collecting, sorting, and processing waste materials and delivering the highest quality recycled base materials possible, stakeholders, including waste management authorities, recycling facilities, and the private sector, must work together.
Utilising chemical recycling processes tailored to input (specific waste streams or materials), and output (raw materials, raw oil, refined petroleum, electricity) is vital. The circular economy can be further strengthened by integrating these processes into existing waste management systems, promoting resource efficiency and reducing environmental impact. By reducing greenhouse gas emissions, managing hard-to-recycle waste streams and addressing the limitations of mechanical recycling, chemical recycling via pyrolysis holds significant potential to significantly support the circular economy.