
As concern for the environment grows, the use of plastic packaging has come under significant scrutiny. The use of throwaway carrier bags, made largely using polymers, has begun to lessen, and global retailers are making a concerted effort to reduce their use of packaging.
Recent figures, however, suggest that campaigns by retailers to cut the number of bags given to shoppers have been met with limited success and are again on the rise. According to official government figures, the average number of plastic bags used a month by each person in the UK rose from 7.2 to 7.7 between May 2009 and 2010, equivalent to 475 million bags a month.
A chemical solution?
There has been much publicity surrounding the floating island of waste, much of it plastic, in the Pacific Ocean. Trapped in the North Pacific Gyre, the latest estimations have measured the ‘great Pacific garbage patch’ to be approximately twice the size of the US state of Texas. One particular solution may rapidly increase the breakdown of such plastics, preventing another waste island of such size from occurring.
Symphony Environmental Technologies specialises in the addition of d2w formulation, which takes the form of a metal salt, to the manufacture of plastics used in bags and plastic packaging. In doing so, the biodegradation can be accelerated and even controlled. The formulation has since continued to be included in a wide variety of packaging and is now used by a number of companies, including the likes of Tesco and SAB Miller, as attempts are made to produce environmentally friendly packaging.
Symphony deputy chairman Michael Stephen, on the back of encouraging financial results, believes that d2w has a definitive place in the packaging manufacturing industry with its ability to provide environmentally friendly plastics whilst maintaining its cost efficiency.
Liam Stoker: How does the d2w technology itself work?
Michael Stephen: The technology itself doesn’t manufacturer plastics as such, but introduces a compound into the plastic product when it is being manufactured. It comes in granules and looks similar to a bag of sugar, but this is the active ingredient.
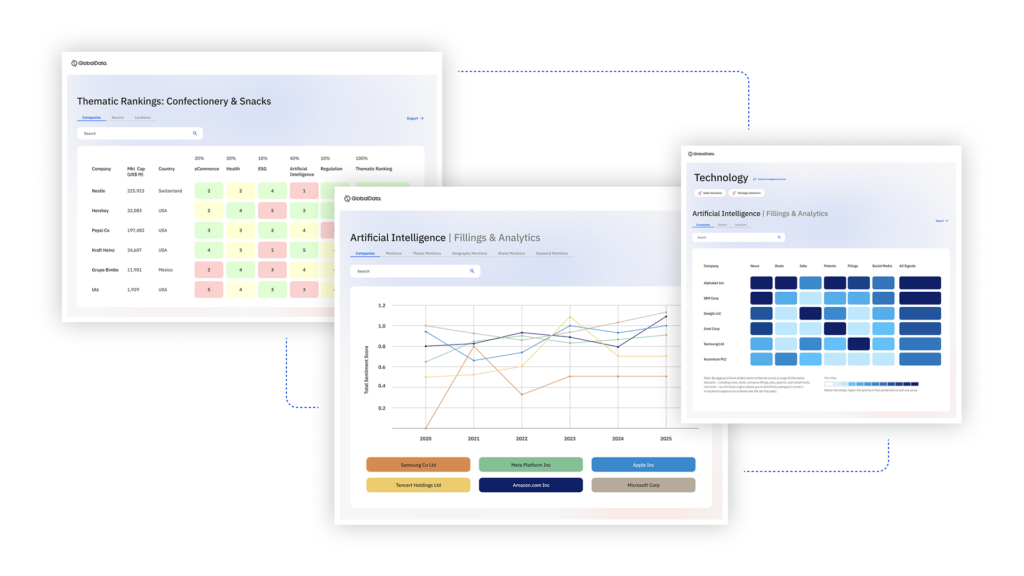
US Tariffs are shifting - will you react or anticipate?
Don’t let policy changes catch you off guard. Stay proactive with real-time data and expert analysis.
By GlobalDataThe formulation is added in either the casting or extrusion stage of manufacture. It causes the plastic to biodegrade when it reaches the end of its life, providing that it is in a regular environment exposed to regular conditions and oxygen.
The way it works is by breaking down the molecular chain of the polymer so, in essence, they are no longer plastics and degrade much in the same manner as leaves. This way, once the bag has had its use it can be left to degrade and its composition resembles that of a leaf, more than a plastic bag.
LS: So, is there a particular shelf life for these particular products?
MS: There is no definitive timescale, as the plastics can be given a pre-determined time frame to biodegrade. We can control this using the formula and it can be specified by the customer. For instance, a bread bag might be used just once and be given a shelf life of six months, whereas a plastic carrier bag could be given a shelf life of six months. We can even extend this into the popular ‘bags for life’ as, after say five years and the handle has fallen off and it’s of no use, we can set the bag to degrade then.
LS: How cost efficient is the technology when compared to traditional manufacturing techniques?
MS: Very cost efficient. Although the desired effects are different, we still use anything up to 99.5% of ordinary plastics in the manufacture process, so the on-cost of our technique can be as little as 0.5%. This is a big reduction compared with something like bioplastics, which can require an on-cost of up to 400%.
LS: Where is the product currently in use?
MS: At the moment, we’re currently active in 92 countries and are working with 67 distributors, as well as some multinational blue-chip companies.
We work with Walmart in three countries, while Volkswagen, Vodafone and Emirates also use our product. Just recently, the brewer SAB Miller has joined as well. All companies carry due diligence on the product itself to ensure that it works as advertised.
LS: Are there any plans to use the product alongside food packaging?
MS: Yes, the product is already used within food packaging. Some of the packaging on frozen food in Tesco stores is produced by us, while we also produce some plastic coverings for magazines.
LS: Do you have any plans for expansion or product development?
MS: We’re expanding all the time with new contracts. One of our latest developments though is the addition of an antimicrobial called d2p, which we can add as an additive to the process in order to make the product bacteria-resistant as well as biodegradable. Some products tend to be handled by many people and can attract considerable amounts of bacteria, but with d2p added into the process they become bacteria resistant.