
The US Food and Drug Administration (FDA) is currently developing an industry standard for the barcoding of pharmaceuticals. However, barcoding of these products has already been initiated in the market. Pfizer is a company that takes a holistic, customer-led approach to this issue and is barcoding its products because it believes that its customers, the hospital dispensaries, will find this increasingly useful.
The company is well ahead of many of the scanning and stock management systems its hospital customers have. A large number of its customers still have to set up the scanning and data management systems to manage the information that can be produced. Most hospital dispensaries still rely, primarily, on the human eye to scan pharmaceutical packs. So, why do the customers want barcodes?
‘The most important reason is to help improve patient safety,’ says Rich Hollander, senior director of packaging services at Pfizer, ‘but there are also secondary, stock control reasons.’
Dispensing errors
Around the year 2000, various factors came together and resulted in an increasing focus on dispensing errors. For example, the Institute of Medicine (IOM) report ‘To err is human: building a safer health system’ was published.
One much-quoted study in the report claims that in the USA, 44,000 deaths a year are caused by medical errors. Another study puts the figure to 98,000 deaths a year. Even using the lower figure means that in the USA, more people die each year from medical errors, than from AIDS, breast cancer or road accidents.
The statistics also show that there has been a three-fold increase in death rates between 1983 and 1993. The expectation is that there will be a ten-fold increase in death rates as the shortage in healthcare professionals starts to bite.
How well do you really know your competitors?
Access the most comprehensive Company Profiles on the market, powered by GlobalData. Save hours of research. Gain competitive edge.
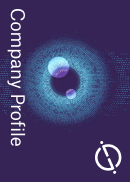
Thank you!
Your download email will arrive shortly
Not ready to buy yet? Download a free sample
We are confident about the unique quality of our Company Profiles. However, we want you to make the most beneficial decision for your business, so we offer a free sample that you can download by submitting the below form
By GlobalDataA Harvard study in the New England Journal of Medicine found that almost half the medical errors discovered in the USA each year (48 per cent) were due to surgical errors. The second most common type of medical error (19 per cent) was medication mistakes. This is where barcoding can make a contribution.
Of course, dispensing errors do not always lead to death. The research shows that barcoding should help to prevent 400,000 bad drug reactions – which can range from headaches to death – over the next 20 years. Barcoding should reduce dispensing errors in hospital pharmacies by almost two-thirds (64 per cent).
In the second quarter of 2001, the National Coordinating Council for Medical Error Reporting and Prevention (NCCMERP) issued a white paper on barcoding for single-dose blister packs. It recommended that the barcode be used for the National Drug Code (NDC), the lot number and the expiry date. It is not yet clear whether the FDA will use the recommendations in this form or will modify them, but a ruling from the FDA is imminent.
‘What was interesting about the NCCMERP suggestion was that for the first time, lot number and expiry dates were specifically mentioned,’ says Hollander. ‘Expiry dates are particularly important because hospital pharmacies manage stocks that they issue to wards; often, stock comes back to them, so they need to know its shelf life. Barcoding would help them manage their stocks better.’
By the end of 2001, the FDA and the United States Department of Health and Human Services were suggesting that all three data elements – NDC, lot number and expiry dates – should be used in the barcodes on unit of use and dose packs.
A research project
What Pfizer is doing, essentially, is extending what it has been doing for more than ten years for its products for the retail market. Since 1992, the company has been barcoding all its retail product packages – a move that was driven by wholesalers, rather than retailers. The wholesalers wanted new and better ways to monitor and control their stocks.
‘For our pharmaceutical business, we started – again prompted by wholesalers, in the form of the Healthcare Distribution Management Association – to put the NDC in barcode format on shipping containers,’ says Hollander. ‘We added case quantity, lot number and expiry date. But this was on cases, not on individual doses.’
By 1996, Pfizer had almost completed the programme. But it was only after the publishing of the IOM report in 1999 that the company’s CEO, Bill Steere, initiated a research project on the use of barcoding on unit-dose blister packs.
Presentation and production
The Pfizer team had to find out in more detail what hospitals wanted. How should the information be presented – in linear, 2D or some other format? What information do hospitals want to find in the barcode? Do they want the existing NDC, which is used for retail products; a new NDC; or the Global Trade Identification Number (GTIN)?
‘The answers we got back towards the end of 2000 indicated that we should produce larger cards to contain the information,’ says Hollander. ‘But this would have significant cost implications for us, since we would have to retool and reduce our throughput.’
So, apart from contributing to the definition of an industry standard for barcoding, Pfizer also wants to mitigate increases in the production costs by minimising the capital investment and the impact that the changes will have on its throughput. The company is also aware that in 93 per cent of US hospitals, there is a lack of scanning equipment to read the data elements in the barcode.
‘Since this information is still monitored by humans,’ says Hollander, ‘it has to exist both in human-readable format and as machine-readable barcodes. We decided that the barcode would have to be readable by conventional barcode readers and that the print quality of the barcode had to meet the American National Standards Institute (ANSI) standards of C or better.’
In the third quarter of 2001, Pfizer presented its solutions. It chose a Reduced Space Symbology Composite Component (RSS/CC) designed by the Uniform Code Council. The RSS14 with composite code was chosen, and it was designed to include the GTIN. There are arguments for the use of true 2D codes, which can contain more information, but the hardware required for 2D barcodes would have had a more significant cost impact on hospitals than the use of RSS, which is read by conventional scanners.
At this point, the greatest technological challenge Pfizer faced was to learn the symbology. The company had to develop a new level of printing expertise since the human eye can make allowances for print variances, for example, which machines cannot.
‘The print quality standards had to be much higher than those we were used to,’ says Hollander. ‘Yet, the readability of the information could not be compromised, because so many hospitals still use the human eye to monitor their stocks.’
Other practical questions the company had to ask itself were: Do we use existing technologies or do we take a giant leap forward? What equipment and what tools do we need, and how can we apply this initiative across multiple sites, on different printing equipment, and in printing with different inks and onto different substrates?
After analysing the problems and researching the solutions, it was clear that one crucial issue was the print quality. The aim was to reach ANSI standards of C or better for print quality.
The company started extensive off-line trial work to find the best ink, print material, roller types, inks and symbology. It also carried out more research into the RSS/CC standard, which has many variants.
Moreover, the company decided it would verify the smallest blister footprint on one commercial line. It opted for a stacked (rather than limited) symbology, but specified that this should not affect the human readability. The smallest size tested was 6.7mil, which represents the width of the thinnest bar, but trials with 8 and 10mil were also performed. The trials, conducted at three different plants, established that Pfizer could meet its ANSI readability target on all but the smallest, 6.7mil, width.
Standardisation
After establishing that the targets could be met, Pfizer took another look at what data to include. The company decided to use the GTIN since that enables the existing NDC to be used.
It then mulled over the concept and practice of application identifiers and decided on a 01 prefix for the GTIN, a 10 prefix for the lot number and a 17 prefix for the expiry date. This way, Pfizer could standardise what it manufactures across the whole company. Previously, individual plants had their own systems for the date format, but now YY/MM/DD has been chosen as the standard within the machine-readable information.
‘Our first lot produced under the new system was released in December 2002. The first product was a 100mg blister pack of Dilantin, an anti-epileptic drug. As human readability is still a vital element, the product name and the strength of the dosage on each blister of the pack are quite prominent.’
‘Initially, people were unable to tell the industry what the barcodes should contain. We recognised the importance of communicating what information our blister packs contain and tried to explain to US hospitals what the implications of this were.’
Inspection and verification
To ensure that its manufacturing systems continue to meet the targets, Pfizer employs inspection and verification. Inspection is the sampling process that checks the barcode by scanning it with a conventional hand-held scanner and reading it. This has various outcomes: the barcode reads properly, multiple scans are required to read the barcodes, it is unreadable or – the worst-case scenario – it delivers the wrong read. This is a critical mistake and may lead to the recall of the erroneously coded products.
Verification is more of a process control operation. It should be built into the printing processes. The barcode is scanned with a verifier, which produces a read-out, giving a quality level according to the ANSI system. It analyses the following nine print characteristics: edge determination, minimum reflectance, minimum edge contract, symbol contrast, modulation, defects, decodability, decode and quiet zone.
The verifier’s read-outs fall into five categories for print quality according to the ANSI standards:
- In the F category, the quality achieved is represented by a numerical value of 0.5 or less, which means that the print is unlikely to be readable on most scanners.
- D scores 0.5-1.5 on the ANSI system and means that the read-out can only be read properly by multiple-path scanners.
- The C category, Pfizer’s minimum target, is between 1.5 and 2.5. These barcodes are more easily read by multiple-path scanners and may require more scans than the top two categories to be read properly.
- The B category, between 2.5 and 3.5, represents good quality, but may mean that the barcode needs a rescan. Single-path scanners can be used.
- The top category, between 3.5 and 4, represents the best quality and is appropriate for single-path scanners.
‘I must point out that although C is our minimum acceptable level, we know that the overwhelming bulk of our output merits an A or a B on the ANSI ranking. We seldom see the C grade,’ says Hollander.
The verifier works by scanning the barcode approximately 250 times. It then randomly selects ten of these scans for analysis.
It analyses the scans to determine the barcode readability and apportions the scan grade according to the poorest grade in any of the scanning parameters (edge determination and minimum reflectance, for example). The overall symbol grade is an average of the ten scan profiles.
Pfizer has learnt the importance of ensuring that only high-quality print materials are used. For its blister packs, the company uses flexographic (flexo) printing, and go from electronic file to film to plate. Codes are verified at each step before the print plate is put into use to ensure the highest quality.
The company has also learnt that it is crucial to keep cleaning the plates so that the image remains sharp; both print materials and rollers must be cleaned frequently. Pfizer has realised that what looks all right to the human eye is not sharp enough for machines.
Future tasks
‘We believe that we have done something important,’ says Hollander. ‘We have supported the FDA and healthcare organisations in their drive towards improving patient safety and have delivered a quality product. We have largely used existing equipment, printing technology and packaging components to deliver the improvement. There has been no significant decrease in throughput, and we could use existing tools and equipment to employ RSS symbology. We have also established standardised package printing systems across the whole company.’
Pfizer is now evaluating the use of alternative print technologies, such as rotary flexo printing using UV curable inks, which afford higher quality printing with less maintenance. The company is also looking at how to be effective in printing these same barcodes on all other products.’US hospitals are scaling up their use of scanning technology,’ Hollander says, ‘and we know that our efforts are appreciated.’
Like the rest of the industry, Pfizer is waiting for the FDA to lay down the rules for barcoding. As the initiator of this change, the company is confident that it is making a leading contribution to what will become the worldwide standard. It is developing an understanding of the requirements in this area globally and developing plans accordingly.