There are clear differences between the requirements for pharmaceutical labelling and labelling in most other industries, where the purpose of applying a label to a container is to decorate and promote. The primary purpose of pharmaceutical labelling, on the other hand, is the unambiguous identification of the contents, in full compliance with the regulatory bodies.
When, for whatever reason, the process of critical identification fails, the consequences can be disastrous. For example, a tragic incident took place in Belgium around four years ago, when two newborn babies died at the university hospital in Louvre, following the incorrect administration of potassium chloride from ampoules that had been labelled ‘glucose’.
Statistics from the US Food and Drug Administration show that labelling mix-up is the second most common cause for a particular product to be withdrawn from the market. Statistics from the UK Medicines Control Agency show the impact of label non-compliance in the 1990s, when there was a steady increase in labelling or label-related mishaps. These statistics clearly show why the pharmaceutical packaging industry must incorporate purpose-designed and purpose-built labelling systems, and encompass greater awareness of these key issues.
Regulatory compliance
To comply fully with the regulatory requirements, it is necessary to verifiy that only the correct product enters the machine for label application. This is of particular importance where the product is filled and sealed in a separate sterile environment, with the product being subsequently autoclaved or chilled, and then stored prior to a transfer for labelling and packing.
Whilst standard operating procedures can be written to ensure that only the correct product is transferred, it can be argued that some form of positive and unique identification should be applied to the pharmaceutical container. Over the years, a number of methods have been adopted, including colour ring code reading, various coloured aluminium caps on vials, 2D matrix codes and a label code.
The next stage in compliance is to ensure that only the correct label is applied to the container. The most common and effective method for this has been to print the label with a unique pharmacode. Similarly, a label identity code – often referred to as an NDC code in North America – can now be read using machine vision adopting optical character verification techniques.
How well do you really know your competitors?
Access the most comprehensive Company Profiles on the market, powered by GlobalData. Save hours of research. Gain competitive edge.
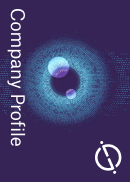
Thank you!
Your download email will arrive shortly
Not ready to buy yet? Download a free sample
We are confident about the unique quality of our Company Profiles. However, we want you to make the most beneficial decision for your business, so we offer a free sample that you can download by submitting the below form
By GlobalDataThe third stage in compliance is to ensure that there is a permanent and legible lot number and expiry date applied to every label. This is typically done effectively using hot foil coding systems, thermal transfer coding or laser. The regulatory authorities expect this code to be legible and complete.
The final stage in compliance is to ensure that every container exiting the labelling system has a label applied to it. This is commonly achieved by using a UV scanning device on the basis that most labels have some form of luminescence in the paper, or that luminescence has been added during the converting process, either as a varnish or in the glue.
All of these security devices must be designed and installed so as to operate on a positive accept principle. In other words, the control system in the labelling system must track every container and every label, and only allow those products for which ‘good’ or ‘accept’ signals are received. Moreover, the overall labelling system must be fully validated.
Validation
Any discussion on regulatory compliance must include the term ‘validation’. Designing machinery with validation in mind makes the whole validation process much easier.
For example, ensuring a well-designed and comprehensively written design qualification (DQ) guarantees that the subsequent installation qualification (IQ), operational qualification (OQ) and performance qualification (PQ) stages of the validation process can all be carried out in less time and with fewer problems.
Typical pharmaceutical standard labelling machinery should be supplied with comprehensive validation documentation. These documents would include: a master plan, DQ, software quality statement, microprocessor control system validation, pre-delivery inspection protocol, IQ and an OQ. It is up to the end-user to carry out the final stage of the validation process, the PQ, using trained operators and ‘live production materials’.