There are six trends that are shaping the way in which GlaxoSmithKline (GSK) manufactures the packaging for its products. In brief these are:
- Rationalisation of manufacturing locations and global or regional sourcing models
- Stricter regulation of packaging processes
- Designing for manufacture
- Global-scale procurement
- Defence of IP, patients and customers
- Shorter lead times for product launch, and automation
Optimisation and regulation
The first of these trends is the industry cost base’s requirement for optimisation, which is leading to rationalisation of manufacturing locations and global or regional sourcing models. As a result, manufacturing sites are supplying an increased range of markets and products, thereby complicating the pack management process.
GSK’s response has been to place greater emphasis on simplifying what it can to create common ways of working and processes, and developing network-spanning communication tools and global or regional centres of excellence.
The second is the increasing regulatory requirements and rigour being applied to packaging processes. Artwork issues are the largest single industry cause for product recall. Consequently, GSK is focusing on ensuring that, where appropriate, processes and systems are robust and validated and meet these new requirements. Establishing a common packaging, generation and change process is helping GSK to remain compliant with the regulators’ requirements.
Designing for manufacture
At present, product development and R&D are becoming more willing to work in collaboration so as to design packaging that is suitable for manufacture and does not add cost to the product.
Post merger, GSK looked closely at the early stages of product development. It created a ‘new-product supply’ board to discuss issues related to the commercialisation of new products. Manufacturing holds a key seat on that board, bringing its technical expertise to the earliest stages of product and packaging design. Overall, the goal of this group is to ‘design for manufacture’ without compromising the need to meet patient and customer demands.
How well do you really know your competitors?
Access the most comprehensive Company Profiles on the market, powered by GlobalData. Save hours of research. Gain competitive edge.
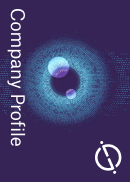
Thank you!
Your download email will arrive shortly
Not ready to buy yet? Download a free sample
We are confident about the unique quality of our Company Profiles. However, we want you to make the most beneficial decision for your business, so we offer a free sample that you can download by submitting the below form
By GlobalData‘Competitive advantage is delivered by enhancing the efficiency of the delivery mechanism to patients, in ensuring patient ease of use, clarity of instruction and appeal of the product, and, critically, in the costs of manufacture,’ says Tim Tyson, president of GSK global manufacturing and supply. ‘It is essential that manufacturing processes are understood and that manufacturing expertise is fed in at the earliest possible stages of the design and commercialisation processes.’
Procurement and related problems
Procurement on a global scale can have a major impact on packaging quality and costs. Indeed, increased attention on this area is already delivering real benefits. Specialists in this discipline are playing a key role early on in the process. Says Tyson: ‘The focus is on cost optimisation by supplying ‘fit for purpose’ and not over-specified materials.’
GSK’s packaging materials suppliers are facing a number of problematic issues, however. As regulators governing the pharmaceutical industry are adopting an increasingly rigorous approach, GSK must ensure that its suppliers are committed to complying with the stringent standards. In this way, the company’s regulatory performance is not jeopardised.
Within the pharmaceutical industry, incorrect packaging components are still one of the main sources of expensive and disruptive product recalls. Moves to electronic artwork transmission and on-line printing and verification are helping to reduce the occurrence of errors in this area.
GSK suppliers are also expected to mirror that company’s focus on lean and Six Sigma processes by taking steps to reduce variability and ensure that their products are of consistently high quality and reliable.
Front-line defence
Pharmaceutical product units can have significant individual value, often saving lives, but they are also vulnerable to tampering. Packaging has a strategic role to play in this area by defending intellectual property, patients and customers.
The fight against drug counterfeiters is a major area where packaging is becoming a strategic issue for GSK. Although overt technologies, such as holograms, may deter counterfeiters, they can be copied. Covert marker technologies, meanwhile, aid detection, especially if used in a multi-layer strategy.
Packaging too is in the front line of defence against product tampering. However, adding tamper-evidence elements increases manufacturing costs and complexity, so businesses need to balance the benefits with the risk. Where tamper-evidence treatments can be of significant value and importance, however, is in the prevention of the refilling of empty vials and bottles.
Looking ahead, additional legislative measures to improve the child-resistant nature of some packs will be factored into GSK’s production and packaging capabilities.
The road to automation
A greater volume of new chemical entities and line extensions to maximise product returns means that lead times for product launch are getting shorter. Packaging suppliers must respond by implementing changes to their products more quickly.
GSK has taken this into account and is increasingly automating pack-change processes with digital workflow tools. It is also introducing range management process development and packaging artwork that makes provision for postponement techniques and late customisation.
Changes in the manufacturing process are affecting packaging too. For example, batch sizes are getting smaller, which is leading to the replacement of higher speed, dedicated packaging equipment with more versatile, quick-change equipment. In addition, as equipment becomes ‘tool-less’ in design, operators rather than technician engineers are being encouraged to perform format changes on a line.
As a result, packaging components must also be simple to allow non-technical operators to manage the activity.
GSK believes that the industry will continue along the road to automation. Additional automated inspection equipment will be designed for the areas of integrity testing, cosmetic defect, missing item and contamination.