A barrier should exclude the entry or exit of water, water vapour and other liquids, while preventing the entry of oxygen, adverse odours and micro-organisms. All of these are usually barred from passage in or out of appropriately sealed containers, such as steel and aluminium cans and glass bottles and jars.
As yet, plastic materials are not capable of imitating the barrier properties of traditional packaging materials, due to economic constraints. However, aluminium foil can form a near-perfect barrier and is sometimes considered a plastic (since it is usually configured with plastic).
Bottle barriers
Multilayer plastic has been a standard oxygen barrier for more than 30 years. Initially, plastic was used to layer barrier materials such as aluminium foil; layered solid structures were a product of this method. However, aluminium foil could not be applied effectively to non-flat structures. So, the search began for ‘barrier’ plastics and similar substances: metallisation and related thin coatings.
The multilayering of plastic remains an effective means to achieve a good barrier. Ethylene vinyl alcohol, co-extruded with polypropylene, has been a mainstream bottle plastic for ketchup, retortable buckets and hot-fill cans since the 1970s. The quest for transparency in ketchup and other condiment bottles led to the genesis of co-injection blow moulding (polyester with ethylene vinyl alcohol) during the 1990s.
Polypropylene remains one of the most effective water vapour barriers, while polyester is chosen for its transparency and physical strength. However, polypropylene has the economic advantage.
The carbonated beverage, fruit beverage and beer markets are demanding ever more effective barriers – all with different needs. Carbonated beverage producers are primarily concerned with preventing the loss of carbon dioxide.
How well do you really know your competitors?
Access the most comprehensive Company Profiles on the market, powered by GlobalData. Save hours of research. Gain competitive edge.
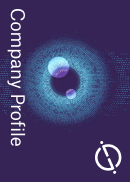
Thank you!
Your download email will arrive shortly
Not ready to buy yet? Download a free sample
We are confident about the unique quality of our Company Profiles. However, we want you to make the most beneficial decision for your business, so we offer a free sample that you can download by submitting the below form
By GlobalDataBeer packagers are concerned with carbon dioxide, oxygen, water vapour, flavour scalping, visibility and heat resistance (because most beer is heat pasteurised). Those who bottle fruit beverages worry about the intrusion of oxygen, as well as flavour scalping.
The most common packaging plastics include polyethylene, polypropylene, polyester, polystyrene and polyamide (nylon). Beyond these, there are some plastics that are used less frequently as a barrier: polyvinylidene chloride (PVDC) and ethylene vinyl alcohol (EVOH). Of the major structural packaging plastics, polyethylene and polypropylene are the most effective, but they are still not perfect water vapour barriers.
Polystyrene has almost no barrier properties, while nylon and polyester are adequate oxygen and water vapour barriers. Of the barrier plastics, PVDC is an outstanding gas, liquid and odour block, and EVOH is an even better oxygen and flavour barrier. However, both have significant deficiencies.
PVDC is the subject of environmental concern because of the corrosion of its hydrochloride content when incinerated, while the moisture sensitivity of EVOH means that it has to be encapsulated within moisture barrier materials such as polypropylene.
None of the common plastics have the barrier properties of traditional packaging materials, such as glass, so scientists and technologists have been seeking more satisfactory solutions. One of the alternatives suggested has been to increase the mass of plastic, which decreases the flexibility of the packaging structure. Obviously, this method is economically undesirable.
Combinations of lamination, co-extrusion and/or coating have been the usual methods of creating more effective barrier plastics. However, these all have their limitations in terms of cost and technical performance.
Modern molecules
In recent years, the search for improved barriers has led to the development of new polymers, polymer configurations, inorganic coatings, thermoset coatings, blending and marriages with active components. The most controversial of these are the new polymers, which are facing regulatory challenges concerning long-term safety. This will undoubtedly have cost implications too.
For example, the introduction of polyethylene naphthalate (PEN) polyester in the 1990s was heralded as a major advance, but the cost increase compared with polyethylene terephthalate did not justify the modest barrier and temperature resistance enhancements. As a result, there has not been another new molecule proposed for barrier packaging over the past decade.
Alternative molecular structures, such as liquid crystals, have shown extraordinary barrier properties. The possible diffusion pathways for gases are effectively closed by tightly packing and aligning molecules. Unfortunately, although some success was achieved in the formation of films and bottles, the final structures were difficult to market commercially.
Coating options
To date, all coatings have been passive (that is, they remain essentially the same, regardless of internal or external environmental influences). The advantages and disadvantages of the current methods available to packagers include:
- Metallisation: The most common coating for plastic structures is vacuum-deposited aluminium. This is usually applied to polypropylene and polyester films to enhance the water vapour and gas barrier by about one decimal.
- Bairocade™: This is a spray-applied thermoset epoxy amine coating from PPG Industries. This coating has been used commercially in Australia by Amcor and Constar on the exteriors of polyester beer bottles.
- Glass coating: Silicon oxide and glass coatings have been applied to polyester and polypropylene substrates to enhance barrier qualities, and give finished products transparency.
- Plasma Enhanced Chemical Vapour Deposition (PECVD): This technology is employed to apply microscopically thin (approximately 40-60nm) layers of silicon oxide onto plastic surfaces.
- Actis: This is an amorphous carbon, which is deposited on the interior of a finished polyester bottle. The coating resists flavour scalping.
- The Japanese plasma nano-shield: This method uses a radio frequency source, along with internal and external electrodes, to ionise the gas. This produces a 20-40nm thick coating.
- Silicon oxide coating: Glaskin produces a coating that can be deposited on the bottle interior by reacting HDMSO with oxygen to form an oxide.
- BestPET: This system uses an evaporative process to generate ions to coat the bottle exterior. Because the coating is relatively sensitive, a secondary coat is applied to the surface.
- Combustion Chemical Vapour Deposition (CCVD): MicroCoating Technologies’ CCVD is able to apply thin coatings at atmospheric pressures. The deposition solution is atomised by MCT’s Nanomiser® atomiser.
Thinner coatings can achieve the same barrier qualities as traditional technologies, but with less product package weight. Plastic surfaces do not need pre-treatment, and still achieve better adhesion than conventional plasma deposition. Exterior coatings have shown better resistance to physical abuse than conventional silica coatings.
Combined efforts
Providing oxygen and water vapour barriers in plastic packaging requires entirely different solutions. This makes it difficult to resolve both issues using the same method. In addition, the flavour barrier has to be resolved in the quest for superior barrier properties for food packaging.
No plastic is perfect, so researchers will have to continue to search for combinations of materials to protect products from environmental influences, while ensuring that the contents are equally securely contained.