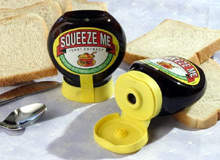
During times of economic uncertainty, innovation can often be the key ingredient for survival. For food manufacturers, packaging design in particular offers a colourful and inventive platform for distinguishing their products from those of the competition.
With the modern-day food consumer market strongly driven by a health and time-conscious population, the need to supply quality products that can be ready for almost immediate consumption is strong.
Furthermore, an increase in single living has pushed food manufacturers to study the value of supplying smaller portions.
Packaging that combines convenience, smaller portions and a dash of innovation has therefore been identified as a successful recipe in current market conditions. Highlighting this is a wealth of new packaging concepts that utilise the latest technologies and materials for fresher more accessible food products.
Marmite – the squeezable bottle
Marmite yeast extract has been a British institution since 1902. It is instantly recognised by UK consumers through its traditional trademark round jar. The standard and custom closures and dispensing systems manufacturer Seaquist Closures was recently commissioned to increase the convenience factor of the product's dispensing system. As a result, Marmite is now available in a round squeezable bottle, which stands top-down on a bespoke yellow cap that has been designed and manufactured by Seaquist.
The company claims that the flip-top closure helps maintain the stability of the tube. The tube also incorporates the SimpliSqueeze silicone valve system for dispensing. When finger pressure is released, the valve reseals to ensure clean product cut-off.
Eatwell – direct film printing
Eatwell is responsible for manufacturing the Feaster range of microwaveable products, including beef burgers, chicken burgers, breakfast baps and hot baguettes. The company recently commissioned Multivac to supply equipment for the on-site manufacturing of trays and is now using the R530 thermoformer in conjunction with the Multivac MR direct film printing system. This enables variable information to be printed directly on the pre-printed film.
A base label is affixed to the pack using Multivac's MR cross-web labelling machine, which labels the pack before it comes off the end of the packaging line. Multivac claims that the new packs are lighter than the premade trays that were previously used. The company also states that the machine can realise an output of 200 packs a minute from a single line. The on-site tray manufacture enables the company to produce the packaging at the same rate as the product. Multivac also believes that one pallet of film for tray manufacturing on the thermoformer equates to 15 pallets of premanufactured trays, thereby reducing warehouse storage requirements.
Dairy Crest – reclosable zipper packs
Dairy Crest has equipped its new factory at Nuneaton with three PFM flow-wrappers to realise zipper-style reclosable packs of cheese portions, principally Cathedral City, its main UK cheddar brand. This is the largest order for PFM zipper packs received to date.
PFM claims that the new BG2800 Zip machines can realise modified atmosphere packs (MAP) of 200g-800g at maximum outputs of 150PPM. The system incorporates a multi-die cross-sealing system that realises approximately ten times the dwell time of conventional MAP machines, according to the company. The reclosable zipper profile can be fed continuously, being incorporated securely in the cross-seals rather than being cut to length and placed between the cross-seal positions.
By working with Dairy Crest and the Dutch project management company VM Engineering, PFM has modified the BG2800 Zip machines so that zipper profile can be added in either continuous or cut-to-length mode. The machines are also able to produce lap-seal reclosable packs incorporating adhesive tape and conventional fin-seal pillow packs.
Hamé – Easy Peel closures
The Czech Republic-based pâté manufacturer Hamé has launched a range of products in two-piece 73mm diameter steel bowls that incorporate Easy Peel closures from Impress.
The company had previously used a standard sanitary end that had to be opened with a can opener, but has since launched four varieties of the 100g containers. Impress claims the bowls convey a 'fresh' image, reminiscent of products found in the chill cabinet. The bowls can also be served directly at the table. The new cans and ends are produced by Impress Znojmo and were launched to the Czech market last year.
RPC Barrier Containers France is supplying plastic cups for a range of products supplied in French school canteens. The local education authorities responsible for running the canteens wanted to introduce new packaging for a variety of food products, including salads and desserts.
They approached RPC Barrier Containers France, which quickly recognised that the white barrier cups would deliver a solution.
Thermoformed in PP/EVOH/PP, which is claimed to provide barrier protection against oxygen ingress for a longer ambient product life, the 80ml and 140ml white cups are filled and sterilised before being closed with aluminium film and labelled.
These examples first appeared on our sister website: www.packagingtoday.co.uk