SSCOM’s Natick Research, Development and Engineering Centre (NRDEC) has unique capabilities for prototyping and testing military packaging systems. This ensures that tests can be conducted on all operational characteristics and functions found in all field conditions. Packaging must protect an item from the time it is produced, through transportation and storage, up until delivery to the ultimate user.
NRDEC’s packaging laboratories are thoroughly equipped to simulate the severe physical forces and extreme environmental conditions that military supplies could be exposed to during the multiple handling, transportation and storage conditions encountered during worldwide distribution and use, from Alaska to Saudi Arabia.
The packaging engineers are responsible for the research, development and engineering support of all technical requirements pertaining to the packaging, packing, palletisation and marking of all food products. The assets of the packaging laboratories include a flexible packaging laboratory, a container testing laboratory and a materials testing laboratory.
The materials testing laboratory tests packaging material for the critical properties of tensile strength, seal strength, water vapour transmission rate and oxygen transmission rate. Once the material properties are established, prototype fabrication is done using equipment located in the flexible packaging laboratory.
Once the prototype packages are made, filled, processed and sealed, packing requirements are developed to include the size, weight and cube of individual shipping containers, the container material and an efficient pallet pattern for a unit load.
This work is done in the container testing laboratory, which is outfitted with test equipment to conduct simulated shipping tests. Rations must meet American Society for Testing and Materials (ASTM) standards for military shipments, including: vibration (repetitive shock), drop, incline impact and compression tests.
How well do you really know your competitors?
Access the most comprehensive Company Profiles on the market, powered by GlobalData. Save hours of research. Gain competitive edge.
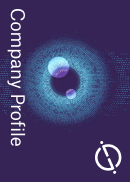
Thank you!
Your download email will arrive shortly
Not ready to buy yet? Download a free sample
We are confident about the unique quality of our Company Profiles. However, we want you to make the most beneficial decision for your business, so we offer a free sample that you can download by submitting the below form
By GlobalDataEnvironmental chambers, located in the container testing laboratory, are used in conjunction with shipping tests for conducting package/container storage studies for packaging material/package testing at environmental extremes. Finally prototype packaging systems are used in production quantities for field testing and, in some instances, aerial delivery with and without parachute assist.
By evaluating the data from this sequence of testing, the suitability of the proposed packaging system can be determined. This results in the safe delivery of mission-essential supplies to our soldiers.
Revolutionary technologies
Revolutionary packaging technologies will be incorporated into current and future ration systems to improve material properties, to validate and protect the food supply, to increase survival rates and to improve overall ration quality. Combat rations will require innovative material and packaging technologies to provide improved shelf life, logistics, quality and safety to the warfighter. Some cutting edge technologies include:
- Nanotechnology: Incorporating nanoparticles into packaging films can improve barrier and mechanical properties.
- Dynamic packaging: Embedded antioxidants and odor- or aldehyde-scavenging materials for packaging films can reduce off-odors/flavors and rancidity.
- Tamper evidence: Mechanical and RFID-based sensor technologies can provide protection against bioterrorism and product tampering.
- Polychromic packaging: Thermo/photochromic reactive polymers that change colour based on the environment.
- Ration reconfiguration: Alternative packing technologies (such as aerogels and airliner) can increase survival rates in worst-case scenarios such as an airdrop.
Nanotechnology
Carried within the meal, ready-to-eat (MRE) packaging is the food that fuels the nation’s military when hot, cooked meals are unavailable. After MREs are consumed, however, the empty flexible packages, which make up one-third of the weight of the MRE, contribute to significant waste problems for the Army.
More than 14,000 tonnes of solid packaging waste are generated annually from the nearly 47 million operational rations consumed by America’s military, according to a report from the Department of Defense Combat Feeding Directorate at the US Army Soldier Systems Center in Natick, Massachusetts.
Environmental research programmes focusing on solid waste reduction exist in the Defense Department, and the Natick Soldier Center has been instrumental in obtaining funding, at all levels of research right up to advanced technology development, for reducing MRE packaging waste. The research is focused on using nanotechnology to develop a new MRE packaging system consisting of nanocomposite film pouches to protect the food.
Current packaging for the MRE entree consists of a retortable four-layer pouch using aluminium foil as the barrier along with polyethylene, nylon and polyester. Other food items, such as crackers, are packaged in three-layer foil pouches. This system can only be landfilled because of the aluminium foil.
The goal of the research is to remove this aluminium foil barrier and replace the pouch with nanocomposite films. Overall, the amount of trash generated from MREs will be reduced because the packaging will be thinner and lighter as well as being recyclable, biodegradable or both.
The MRE’s shelf life is three years at 80¼F and six months at 100¼F. With such stringent shelf life requirements, an exceptional barrier material is necessary. The packaging also needs to be robust enough to withstand airdrop and rough handling associated with the military logistics system.
The outer meal bag that holds all the individual components is made from a thermoplastic polyolefin, but is thick to resist burrowing insects. MREs also suffer from flex cracking or pinholing in the foil-based laminates, when exposed to cold weather.
To reduce packaging without sacrificing performance, engineers at the Natick Soldier Centre are investigating various recyclable thermoplastics and biodegradable polymers blended with nanosized fillers. Nanocomposite food packaging is a potential solution for food preservation because of the high oxygen and moisture barrier properties of films containing nanosized platelets.
With polymer nanocomposites, not only are the barrier properties improved when compared with the pure or neat polymer, but the mechanical and thermal properties improve as well. This could improve structural integrity during handling at the manufacturer as well as when the MREs are exposed to cold weather during storage.
If used in the outer meal bag, nanocomposites could potentially replace high barrier foil laminates used for MRE components. Removing the aluminum foil barrier layer dramatically improves potential for disposal and recycling. Polymeric packaging systems also can be thermoformed with a deeper configuration, enabling multiple items to be cluster-packed to eliminate redundant overwraps and paperboard cartons, thus reducing weight and volume.
A research team at Natick has formulated and produced polymers with a 1-5 per cent clay platelet mixture by using in-house twin screw and blown film extrusion equipment. In the extrusion process, chemically treated clay platelets are mixed into the polymer to maximise clay dispersion and orientation. The surface of the clay platelets is modified in order to incorporate it into plastic resins on a nanoscale size – one billionth of a metre. This is 1000 times smaller than conventional additives or composite material fillers, such as starch.
Because nanoclays contain so many individual particles in a relatively small amount of material, it takes a low percentage of clay to obtain a high concentration of constrained areas within the polymer, which lowers bulk and weight. The clay platelets disrupt the diffusion path of the oxygen and water molecules. The better the barrier, the more tortuous the path is through the polymer chains.
Nanocomposite qualities
Research has focused on materials such as polyethylene, polyester and ethylene co-vinyl alcohol (EVOH) nanocomposites. The low-density polyethylene (LDPE) has obtained an 80¼C increase in thermal stability and a 100 per cent increase in Young’s Modulus. A biodegradable nanocomposite consisting of polylactic acid (PLA) has decreased the water vapour transmission rate by more than 200 per cent compared with pure PLA while also significantly increasing mechanical properties such as toughness and modulus.
The EVOH nanocomposite achieved the oxygen barrier requirement for the MRE. However, these properties are dependent on temperature and humidity. Currently, EVOH nanocomposite layers are being sandwiched in-between LDPE using a new in-house co-extrusion line to make multilayer films.
Nanoclay materials in MRE production are projected to cost 10-30 per cent less than current foil-based laminate materials, with a projected total life cycle cost saving esti- mated at $1-3m. Nanocomposite films showing the most potential will be tested, downselected, further evaluated and compared with the existing MRE packaging to determine compliance with military requirements.
The films will be further evaluated by the advanced processes and packaging team for compatibility with novel advanced food processing technologies that are incompatible with current high-barrier foil laminates. From there, the individual and group rations teams will take over on the way to the manufacturing and procurement of the same warfighter-tested, warfighter-approved product with reduced packaging waste.
Packaging applications
Polymer nanocomposite technology refers to the dispersion of high-aspect ratio gas-impermeable silicate or natural clays in a polymer matrix. This technology is being investigated to improve barrier, mechanical and thermal non-foil properties of food packaging films.
There is a need to develop a high-barrier, non-foil material for ration component packaging systems. Current polymeric materials do not provide sufficient barrier properties to satisfy military requirements. Nanocomposite films are being investigated to improve both barrier and mechanical properties.
The development of environmentally-friendly, non-foil packaging, and the evolution of improved packaging concepts will significantly reduce the amount of solid waste, improve package manufacturing capabilities and reduce the overall logistics burden (weight and cube of rations) on the warfighter.
High-barrier, non-foil materials are being engineered for ration packaging systems with improved barrier properties and package survivability through the incorporation of nano-clay particles into thermoplastic resins.
Pouch bread
This product emerged as a technological breakthrough during Operation Desert Storm. Fresh, shelf-stable bread packed in a pouch. The special formulation allows the pouch bread to retain its quality during long-term storage – even at high temperatures.
Pouch bread has evolved into a highly desirable component of soldiers’ meals. Recent improvements to the bread include adding new ingredients, revising the existing formula and processes, and improving the packaging. Together, these novel ingredients and technologies allow pouch bread to be stored for a minimum of three years – while preserving its flavour and nutrient content Some of the ingredients and technologies in pouch bread include:
- Preservatives that prevent the growth of microbes
- Bread stabilisers that produce a tender crumb and reduce staling
- Water-control agents that control water activity in the bread to keep it stable and extend its shelf life
- Oxygen-scavenging sachets that maintain low oxygen levels in the pouch to protect quality
- Novel packaging materials that provide additional quality protection
Institution-sized pouches
Commercial packaging technologies are being investigated to help get longer lasting, higher quality group rations to warfighters in the field. One such product is the institution-sized pouch (ISP). The ISP can hold many pouch-compatible items, such as fruits, vegetables and stews, and is suitable for use in field feeding environments.
Many group-serving ration components are packaged in the #10 can, a polymer-coated metal container that may degrade and rust under harsh storage conditions. The military services desire a package that would hold the same types of products, last just as long or longer, taste fresher, and be safer and easier to open and use.
The ISP is constructed from a reinforced flexible laminated film structure that allows it to withstand the rigours of military distribution. The thinner profile of the ISP allows for reduced processing time and better overall product quality. Working with ISP producers enables expansion of the military vendor production base.
All these technologies bring great advantages to military operations. However, most of them will translate well into commercial packaging situations, as consumers want much the same things.