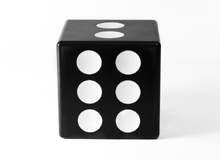
Six Sigma is a business management strategy that was introduced in the US by Motorola in 1981 and is now deployed across a wide range of sectors, including the packaging industry.
Having enjoyed early success with the likes of General Electric and Honeywell, varying forms of Six Sigma were deployed on a wider scale in the late 1990s and have most recently been practised in conjunction with Lean – a production practice that focuses on eliminating all waste from the production chain.
Six Sigma projects tend to follow two main methodologies, which comprise five phases each – DMAIC, which is used for projects aimed at improving an existing business process and stands for define, measure, analyse, improve and control; and DMADV, which is aimed at created new product or process designs and stands for define, measure, analyse, design and verify.
The strategy’s name derives from the notion that if one has six standard deviations between the process mean and the nearest specification limit then practically no items will fail to meet specifications. This calculation method is employed in process capability studies which are often implemented by Six Sigma consultants, such as LCP Consultants.
Alex Hawkes: What is the main ethos of Six Sigma? And how does it work in tandem with other production practices such as Lean?
Julian Mosquera: Six Sigma and Lean are both essentially a mindset and collection of techniques deployed to investigate and resolve a given problem or business issue. Six Sigma has evolved from what was originally a single technique designed to manage process variability – at the heart of this philosophy is the idea that making processes more predictable and reliable leads to increased quality, improved yield and less waste. Lean, on the other hand, has a strong process
engineering background with its central focus on waste reduction in all its forms.
Both effectively look at the cause and effect around a problem, establishing its magnitude and means of managing or eliminating it altogether. Both have adopted each other’s “techniques” – so Lean now encompasses Six Sigma, which has itself moved from being a single technique to becoming a programme and mindset. Purists would still argue they are fundamentally quite different, but I believe that, on the ground, they are applied in very similar ways.
AH: What are some of the typical issues a Six Sigma consultant will address at a company?
JM: A great deal of Six Sigma projects are currently focused on reducing inventory and cost, but the focus is necessarily becoming more ambitious.
Projects typically use five or six analytical techniques from the Six Sigma “toolbag”. Companies need to be selective about the sort of tools they use and think carefully about how the result will be reported.
One of the things we do at LCP Consulting is establish from the outset what the expectations of a project are, recognising and understanding how the holistic organisation may be affected. Often, with a strictly Six Sigma or Lean approach, the scope is quite narrow and solutions can fail to embrace the wider organisational implications.
Whatever approach is taken, it should be about getting to the heart of a problem rather than just addressing the visible symptoms. In some cases, this may only require changing the decision-making protocol or the parameters in a system. What can initially seem like a big problem can turn out to be quite easy to address and, of course, what seems small can mask a much deeper issue.
AH: What are some of the potential drawbacks of embarking on a Six Sigma or Lean programme?
JM: Six Sigma and Lean programmes can involve a heavy resource commitment; for instance requiring companies to invest in extensive staff training. These programmes are sometimes criticised for overwhelming the business – consuming time and resources without necessarily delivering on the promise of a significant cost reduction. Six Sigma projects often run for up to nine months as part of the investigation and solution definition phases, which I believe is simply too long.
What LCP would rather do is run what we call a health check (or RapiSCAN), which gets to the nature of the issue and an action plan in the space of six to 12 weeks depending on the problem under review. As a result, we still deploy many Lean / Six Sigma techniques and thinking, but without the overheads.
AH: Six Sigma uses a set of quality management methods that create a special infrastructure of people within an organisation who are trained to different levels of expertise in these methods. What are your thoughts on this?
JM: When a business first embarks on a programme, it typically identifies a small elite group that should be capable of running such a programme (black belts) and a support group (green belts). Both need a significant period of training in the basic techniques, with black belts immersed in their application and interpretation to yield appropriate solutions for a business to implement.
Whilst there are companies for whom this heavily formalised approach is relevant, I believe the process is too long. Staff with some initial training and orientation applied directly to a business issue can learn from a consultant on the job. For us, it is therefore about constructing a programme and engaging a business as early as possible in deploying the problem solving techniques.
It is important to maintain the competence of the internal team and have sufficient projects to keep them busy over the long term to justify the initial investment.
A slightly different perspective relates to the project focus. The pool of projects to be investigated is usually created by managers, more senior than the black belts, who will not have received the same rigor of training. So the black belts’ success is determined by the senior management group’s capability to jointly manage a programme that delivers against the strategic needs of a business while being grounded in real issues that need to be addressed.
AH: How large should an organisation be in order to deploy an effective Six Sigma project?
JM: There is no denying that over the last two decades, larger organisations have tended to be more likely to have the resources and depth in manpower to deploy a comprehensive Six Sigma programme. A multinational or global organisation will have business processes that cover multiple countries or functions. Quite a few global businesses develop in-house Six Sigma teams, which would not be financially viable for a small to medium-sized enterprise.
Even in a sizeable company the pool of talent available to become “black belts” is limited and it takes time to build up the expertise. Where capable people exist, they often have limited experience outside the operations they find themselves in. Though training is extensive, it tends to be intensive over a short period. Some are able to absorb and apply, while many cannot, and find themselves depending on a small number of techniques. When it comes to challenging the status quo, internal
resources can have a tough time persuading more senior managers to change direction. Six Sigma is a good tool, but inevitably has some limitations.
Six Sigma projects, however, can be deployed effectively in any size of company, but a different approach is needed for smaller businesses. Here it is generally a case of going to a specific factory or country operation, undertaking an investigation and implementing the solution locally. For this size of business, a combination of learning the skills and working with a consultant to develop new skills proves to be of greater value. When this approach is applied to specific projects it often
leads to better results, and value is delivered much earlier to the client.
Therefore, a Six Sigma project can be deployed effectively in any size of company. The smaller the company though, the more difficult it is to group together the skills and know-how. The wider challenge is to not to just deploy a project but to deploy a rolling programme so that the approach to projects becomes one of utilising statistical techniques and good project management disciplines, which in turn becomes a business habit.
Part of the ethos of Six Sigma is to recycle the black belts so that they are reintroduced to operational roles, ensuring that the background capability of the organisation is enhanced and better Six Sigma governance develops. Most organisations find that this is a difficult progression and takes considerable time. External injections of expertise can be beneficial to Six Sigma, introducing a different perspective gained from experience within other organisations. This can also provide
additional resource and focus to enable a boost to getting effective change implemented.
AH: How has the global economic downturn affected general attitudes towards Six Sigma and Lean?
JM: Industries now face a different problem when it comes to risk. While improving a process to ensure it is more predictable can only be a positive move, the flipside is that if you remove all of the residual capacity from a business then, by definition, it becomes inflexible.
What we have found with the economic downturn is that those unable to respond to very short-term needs, such as customer demand, have placed their business at risk.
This issue is currently being debated in the commercial functions, where questions are being asked as to how companies can effectively manage risk or be more flexible, or how supply chains and manufacturing operations could be designed to better respond to such short-term changes in demand. Six Sigma and Lean projects are now starting to address these challenges.