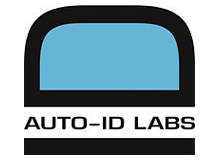
Radio Frequency Identification (RFID) systems have been in commercial use since the mid-1970s. From their humble beginnings in livestock identification, RFID systems have found uses in a broad range of applications. From pet identification and access control to automated toll collection and immobilisation systems, RFID has become commonplace in our lives, providing tremendous benefits through automation.
The potential benefits obtained from the use of an RFID system will continue to drive their adoption in new application domains, solving problems that most people didn’t know existed. The price of the tags is the primary determinant of the speed of adoption for a specific application. The lower the cost of the tags, the greater the number of applications for which RFID systems became economically viable.
The most recent application to admit RFID technologies is supply chain management. The largest logistics organisations in the world, Wal-Mart and the US Department of Defense (DoD), have begun using RFID systems to improve their supply chains. The adoption of passive silicon-based RFID systems within their supply chains was driven by the emergence of a single passive RFID standard that reduced the tag costs below $0.05.
There are two basic components that make up the cost of an RFID tag: non-recurrent engineering design costs and tag manufacturing costs, which includes silicon, antenna, substrate, silicon-antenna attachment, and tag packaging costs. The volume of tags demanded by just Wal-Mart and the DoD will eventually exceed several trillion tags annually. This will make the engineering design costs effectively zero per tag. Consequently, the price of the tags will be based on the manufacturing costs.
Tag manufacturing today
The lowest-cost silicon-based passive RFID tag is a passive tag packaged as an adhesive label, often referred to as a ‘smart label’. This smart label is comprised of at least five basic components that are assembled in at least three unique manufacturing steps.
The five basic components of a smart label are the substrate on which the tag is assembled, the antenna used for power harvesting and communication, the silicon chip containing the functionality of the tag, the material connecting the chip and the antenna, and the paper label adhesive packaging for the tag.
The three manufacturing steps are the antenna manufacture, the connection of the chip to the antenna and the conversion into a paper label.
A thin plastic sheet, or substrate, forms the foundation of the smart label and is the first basic component of the tag. The substrate is flexible and uniformly smooth making it amenable to a wide array of metal lithography, metal etching, metal stamping, and printing processes that can be used to manufacture the antenna.
Metal etching is the most commonly used method of creating an antenna. It works by covering the entire substrate with a thin (approximately 35µm thick) sheet of metal, typically aluminium or copper. The desired antenna pattern is masked out and all excess metal is removed. Since etching is a subtractive process, complex and widespread antenna patterns require a large amount of metal and, consequently, are more expensive than simple designs.
The silicon chip provides the functionality of the smart label. The antenna enables communication between the label and a reader. The chip must be securely connected to the antenna, with significant electrical connectivity to enable efficient power harvesting and communication. The chip is connected to the antenna with a conductive adhesive, such as solder or a conductive epoxy.
The most widely used manufacturing method for placing a chip on an antenna is flip-chip assembly. This technique involves placing the silicon chip directly on the antenna. The conductive adhesive between the chip and the antenna ensures that the connection is robust.
The assembled substrate, antenna and chip are then converted into a final packaged form to become a discrete tag. The tag is applied to the object that it will be used to identify.
Towards low-cost tags
The greatest benefits, particularly within supply chain management applications, made possible by the application of RFID technologies will be realised only when nearly all objects are tagged. The greatest barrier to the ubiquitous RFID tagging of objects is the cost of creating a tagged object. Just as when bar codes were first introduced, the ‘new’ cost of tagging an object is both a psychological and economic barrier to tagging all objects for all applications.
For most objects, particularly high-cost and high-margin items, this tag cost barrier is five cents (cost with the tag applied to the objects). For tagging all items, the tag cost barrier moves closer to zero. Therefore, it is important to minimise the applied tag cost to enable the greatest number of applications and receive the greatest benefits.
Each tag component and manufacturing step adds to the tag cost. Only by minimising the number of components, the cost of each component used, the manufacturing costs and the tag-product integration costs can the lowest cost be achieved.
There is little flexibility in the simple passive tag components list. The silicon chip, the source of functionality for the tag, must be present. The antenna is required for communication and energy harvesting. The connection between the chip and the antenna is required for the tag to function. All other components and the manufacturing steps used to create the tagged object are dependent upon the materials used to create the antenna and the manufacturing technology used to assemble the chip and the antenna. The cost of all components and processing steps must be minimised.
The chip cost is determined by volume and chip size. High-volume silicon chips have historically experienced an average total production cost (including manufacturing, wafer testing and separation costs) of four cents per square millimetre. Therefore, chip-cost is minimised by reducing the chip size.
Chip size is directly proportional to the amount of functionality implemented on the chip. Simple identity tags clearly will yield the lowest cost chips.
The tag antenna is required for communication and energy harvesting. As such, it must be made of highly conductive materials. The traditional use of metal for antenna material is relatively expensive due to material cost, the requirement for a smooth substrate (such as PET) on which to manufacture the antenna, and the requirement for a clean manufacturing environment. Using a less expensive conductive material and/or reducing manufacturing requirements may reduce antenna costs. Conductive inks, inks with high electrical conductivity properties, may be used as the antenna material for RFID tags.
Many conductive inks are used today as the antenna material in RFID tags, and they have proven to be capable and cost effective. As the price of conductive inks continues to decrease, they will become the antenna material of choice for low-cost RFID tags.
The use of conductive inks enables the antenna to be printed directly on an object, such as the product packaging. The chip can be attached directly to this antenna. Thus, a tagged object may be created without creating an inlet or a discrete tag.
The ultimate in low cost tags will be achieved when the functionality of the silicon chip may be printed directly on the object as well as the antenna. Such tags are emerging in the high-frequency (HF) spectrum used for short-range communications, but are still being researched for the ultra-high frequency (UHF) spectrum used in the tags mandated by Wal-Mart and the DoD.
Conducting the changes
Conductive inks contain particles such as silver, carbon, and/or other semiconductive materials. The conductive particles are held in a non-conductive retaining matrix such as a ceramic or a polymer (known as polymer thick film (PTF). The particles are able to conduct electricity only when they are in contact with one another. A curing process must be applied to the printed antenna or circuit to remove the PTF barriers between conductive particles.
Curing is often performed either by exposing the ink to ultra-violet light or to a minimum temperature for a period of time. Many ceramic mixtures require a high curing temperature, often in excess of 600ºC, with a minimum exposure time of 30 minutes or more. These curing requirements limit the types of substrates that are amenable for use with ceramic-based conductive inks.
In contrast, PTF mixtures have significantly lower curing temperature requirements, typically around 100ºC for 30 minutes, to achieve maximum conductivity. Low-cost plastic substrates, such as PET, are amenable for use at these temperatures.
The curing temperature is dependent upon the ink formulation and the degree of conductivity required for the application. Some conductive ink formulations dry quickly at 20ºC, but have reduced conductivity compared to those cured at 100ºC. UHF RFID tag antennas do not require the maximum achievable conductivity to be effective.
Just as the substrate on which ink is printed affects the appearance, the substrate on which conductive ink is printed impacts the achievable conductivity. Smooth surfaces such as glass and PET enable the greatest possible conductivity. Rough surfaces, such as that exhibited by newspapers and untreated cardboard, enable a significantly lower maximum conductivity.
Conductive inks are commercially available in formulations suitable for a range of printing processes such as flexography, gravure, lithography, screen, and rotary screen, and substrate quality such as kapton, mylar, glass, PET and some coated papers.
They are widely deployed in thick film circuit fabrication processes in the manufacture of electronic circuits, systems, and components. The most common thick film fabrication technique uses screen-printing to deposit the ink onto either rigid or flexible substrates. Screen-printing is able to create patterns that are approximately 25 microns in thickness. The resulting patterns are cured. Resistors may be formed by using ink formulations that yield a finite resistance when they are cured. Thick film circuits are extensively employed in high-reliability and aerospace applications.
High-speed printing techniques, such as lithography, are more economical than screen-printing for high-volume printing applications. High-speed printing techniques can be used at up to 2000ft per minute on wide web platforms. A 20-micron resolution is achievable with many high-speed printing techniques. Lithographic printing is able to produce an antenna that is approximately 3µm in thickness. This reduces drying time with negligible impact on the performance of the tag as compared to traditional metal antennae.
Due to the performance advantages of larger and more complex antenna designs, they are preferred to basic antenna designs such as folded dipole antennae. Printing these minimises waste products, making them cost-effective, and they perform better than the basic antennae.
The ability to vary the conductive and other electrical properties of inks has lead to the development of printable, functioning electronic circuits. RFID tags promise to become extremely cheap when all functions can be printed. They can be printed under the standard temperatures and pressures that exist in a printing operation or production facility. Therefore, organic semi-conductive materials must be used in printed tags.
Currently available organic semiconductive materials are not very robust. They are susceptible to a wide range of environmental constraints such as temperature and humidity. Additionally, they offer relatively low electron mobility. This only allows low switching speeds, somewhere in the kHz range. This is sufficient for the operation of an HF RFID tag, but an effective UHF RFID tag requires switching speeds in excess of 1GHz.
A positive future
Conductive inks promise to enable a plethora of new RFID applications by allowing for low costs when creating tagged objects. RFID tags are being deployed in large volumes, but the more objects that use RFID tags, the greater the benefits that may be achieved across the spectrum. These inks will allow standard printing techniques to be used and therefore substantially lower costs. There is no doubt that this is one technology that will boost an already growing area.