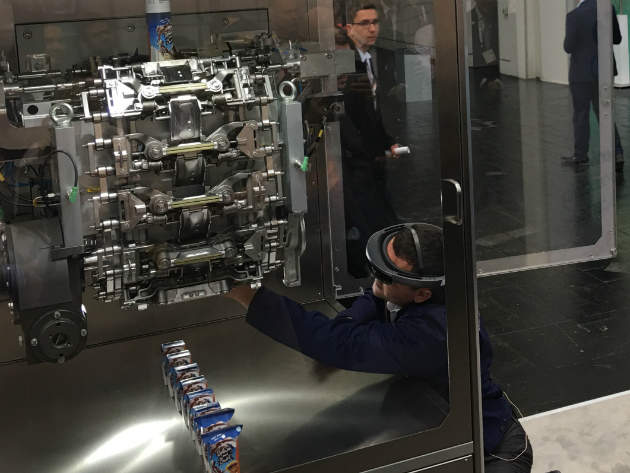
Digitisation is the future of the food and beverage packaging sector; that was the message being pushed at Tetra Pak’s presentation in collaboration with Microsoft at Hannover Messe 2017. The packaging giant was keen to discuss how it is developing the workplaces of its clients, making use of new technology to improve the efficiency of equipment, as well as the workforce.
Sitting in the crowd in the Tetra Pak booth, within the Microsoft section of one of the mammoth Messe exhibition halls, it was easy to see Tetra Pak’s anticipation about the forthcoming digitisation announcement, though it became apparent that specific details were a bit more sparse than expected considering the gravity of the event.
Tetra Pak vice president Johan Nilsson wanted first to make clear the safety aspect of digitisation within packaging, perhaps to allay the fears of more sceptical clients. He stated: “We commit to making food safe and available everywhere, and the food safety aspect is a very key component when you digitalise manufacturing.”
However, the crux of the announcement revolved around the themes of a ‘connected workforce’, ‘advanced analytics’ and ‘connected solutions’.
A connected workforce
Tetra Pak made clear the link with Microsoft by demonstrating its adoption of HoloLens technology as a key aspect of the ‘connected workforce’ concept. In addition to connecting workplace employees through the use of established technology such as smartphone apps to deliver maintenance alerts and performance information, Tetra Pak has begun to roll out the use of HoloLens augmented reality (AR) headsets.
The basic idea is that when an engineer is fixing a faulty machine and cannot solve the problem themselves, they can call up a specialist via the headset’s Skype functionality. The specialist would be able to see what the engineer sees and help fix the problem as soon as possible, even using AR functions such as highlighting the faulty part on the HoloLens screen for the engineer.
“It’s a very easy transformation from the engineer’s point of view, it helps them,” says Nilsson. “If I, the engineer, can’t help you then within three minutes I can get help to solve the problem, instead of perhaps working for 48 hours and not being able to solve the problem.”
One could perhaps make the argument that an engineer trained to solve such problems should perhaps not rely too heavily on such calls. Of course not every engineer will be able to solve every problem, and the technology will of course help with that, but it could also be seen as a very expensive option for what could be considered a last-ditch catch-all measure.
Predictive maintenance
The other key announcement fell into Tetra Pak’s categories of ‘advanced analytics’ and ‘connected solutions’. The company hopes, as far as possible, to eradicate the costly failure of machines in its customers’ factories through the analysis of data collected from said machines.
Tetra Pak machines are being set up to send data back to a ‘media centre’, which will allow accurate predictions to be made as to when a machine or part is in danger of breaking down. All of this data can then be sent back from the media centre to the client, as well as being used on Tetra Pak’s side for optimisation purposes when new packaging machines are under development. If a key component breaks within a packaging manufacturing chain, which can sometimes last days and affect potentially hundreds of thousands of unpackaged items due to the scale of some machines, it can cost the client a very large sum of money.
Speaking about the scale of the data received, Nilsson stated: “We have around 10,000 packaging lines in the world, and a packaging line typically consists of around four to five pieces of equipment, so that’s 50,000 pieces of equipment, and we also have around 50,000 pieces of processing equipment. Of those 10,000 lines, 60% are connected and send data today. There is still around 20% that can be connected, but in some cases we have [machines that are] 30-40 years old, so there is a limit in what makes sense. But everything new we make sure is connected.”
Predictive maintenance is not a novel idea, but it is certainly encouraging to see Tetra Pak engaging with the concept so wholeheartedly.
It is worth noting, though, that while much of the information that came out of Hannover Messe was promising for the future of the packaging workplace, the dark cloud of automation was not touched upon. It is understandable why Tetra Pak would be excited about such digitisation developments, though if it truly wants to allay fears surrounding the digital workplace, the matter of potential human redundancies due to automation and artificial intelligence will need to be addressed somewhere along the line as the company continues to roll out its digitisation strategy.