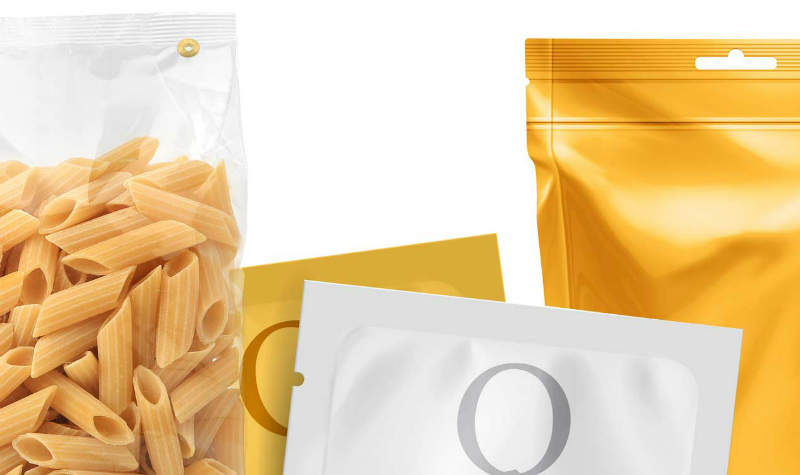
A consortium of European companies has set up a project to increase flexible packaging recycling rates. Katie Woodward finds out how this how this initiative can fast forward the recycling stream.
The CEFLEX project is the collaborative effort of a European consortium of companies, including Unilever, PepsiCo and Nestlé, representing the entire value chain of flexible packaging. The project was launched following concerns that the hard-to-recycle waste stream is not being properly dealt with. Flexible packs are often made from laminated layers, which can be difficult to separate, causing problems when it comes to recycling this type of material.
According to the CEFLEX website, the project has “the ambition to make flexible packaging even more relevant to the circular economy by advancing better system design solutions, which results from the value chain collaboration of the consortium.” The ultimate aim is to develop a collection, sorting and reprocessing infrastructure for flexible packaging across Europe by 2025.
The project: helping the circular economy
Launched in January 2017, CEFLEX – or a Circular Economy for Flexible Packaging – follows on from another Europe-wide packaging project, FIACE, which highlighted the significant contribution flexible packaging makes to the circular economy and identified opportunities to optimise end of life solutions.
Initially, the CEFLEX project stakeholders will focus on seven main workstreams in 2017/2018: design guidelines for flexible packaging in a circular economy; understand and map the European market; identify and develop sustainable end markets for secondary materials; develop a sustainable business case for collecting all flexible packaging; show proof of principle in the pilot region or country; and facilitating technologies. CEFLEX will build on the work carried out under the FIACE project, with a particular emphasis on the recyclability potential of flexible packaging.
Barriers to recycling: a range of materials
Currently, the main issues with flexible packaging are related to end of life challenges. Although it is a resource efficient packaging format, it is made up of a range of materials – including polyethylene, polypropylene and non-polyolefin laminates – which must be separated before the package can be properly recycled. In the UK alone, every year a total of 414,000 tonnes of plastic-based flexible packaging is placed on the market – and after use, most of this material is disposed of in landfills or incinerated to recover its energy content.
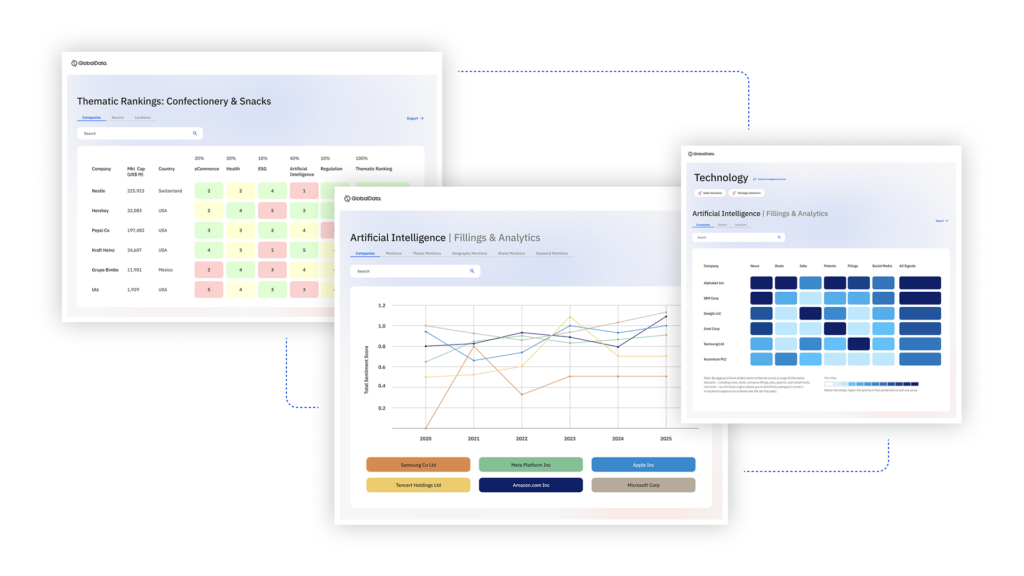
US Tariffs are shifting - will you react or anticipate?
Don’t let policy changes catch you off guard. Stay proactive with real-time data and expert analysis.
By GlobalDataHowever, existing end of life challenges to recycling flexible packaging include collection (the waste material is not yet widely collected for recycling in all European countries); technical (the combination of different layers and materials makes it more challenging to recycle than single-material packs); and infrastructure (the light weight of flexible packaging means more packs need to be collected to meet weight-based recycling targets).
Next steps: end of life challenges
The CEFLEX project stakeholders will look to address these end of life challenges with the ultimate aim to develop collection, sorting and reprocessing infrastructure for post-consumer flexible packaging across Europe by 2025. Graham Houlder, project coordinator, says that the vision and activities initiated by the project should deliver significant gains by 2020. “We expect more flexible packaging to be collected and recycled in an increasing number of European countries,” he explains. “Also there will be recognition of the significant value this packaging format adds to the circular economy through measurable resource efficiency, waste prevention and recycling benefits.”
Some of the 34 project stakeholders have already made inroads into addressing some of the end of life recycling challenges. Michael Scriba, managing director of mtm plastics, adds: “We have already developed successful techniques to separate and sort mixed materials. These need to be improved and expanded. In addition, and equally important, there is a need to further develop and establish financially sustainable end markets for secondary materials from flexible packaging.”
Innovative initiatives: UV light detection
Project stakeholder APK, which manufactures high-quality plastics, plastic mixtures and compounds, and treats packaging waste, announced earlier this year that it will set up five recycling plants by 2025 in Europe and South East Asia to strengthen plastics recycling and reduce litter. The company has developed a breakthrough technology that can be applied to a wide range of plastic types used in flexible packaging. The technology, dubbed Newcycling, exploits physical and chemical properties of different polymer types in order to separate the multi-layer films in flexible packs, resulting in high-purity single-polymer streams, which can then be recycled in their respective waste streams.
In the UK, another technique uses invisible phosphor inks to label plastic packaging, which can then be detected by UV light. Developed by Brunel University London, the new technique called PRISM (Plastic Packaging Recycling using Intelligent Separation Technologies for Materials) coats a transparent phosphor ink onto the product’s label before use. Current recycling technology is able to detect the luminescence from the phosphors, and can identify the material of the plastic as well as what was contained within the package.
In addition to commitment from manufacturers, the PRISM technology requires the addition of a UV source to existing near-infrared sorting systems, which can be programmed to read the phosphor codes. The initial full-scale trial, carried out by Tomra Sorting, showed the technique collected 98% of labelled plastics with 95% accuracy. Dr Paul Harris, research fellow at Brunel, explained what this means for flexibles recycling: “It will mean a larger proportion of waste will be identified and recycled, rather than going to landfill. The system is working a treat and we have already had lots of international interest. The next phase is to get the costs down, but the process works, there’s no doubt about it.”