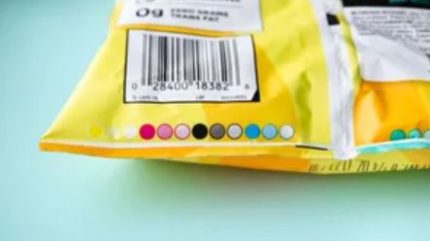
If you’ve ever noticed a row of small, colourful circles or squares on the edge or bottom of your food packaging, you’ve likely stumbled upon what’s known as “process control patches” or “printer’s colour blocks.”
Though they often go unnoticed by consumers, these dots serve an essential function in the packaging industry, ensuring the print quality of the packaging itself.
What are process control patches?
Process control patches, commonly seen on food packaging, are colour reference points used during the manufacturing process to guarantee consistent print quality.
These blocks, usually displayed in a range of colours like cyan, magenta, yellow, and black (CMYK), allow printers to monitor how accurately the machine is reproducing the intended design.
By comparing the actual output with these reference patches, any colour imbalances or imperfections can be detected and corrected quickly.
For instance, if the red hue on a package is not printing correctly, the colour blocks can indicate whether it’s the magenta ink that’s too heavy or the yellow ink that’s too weak.
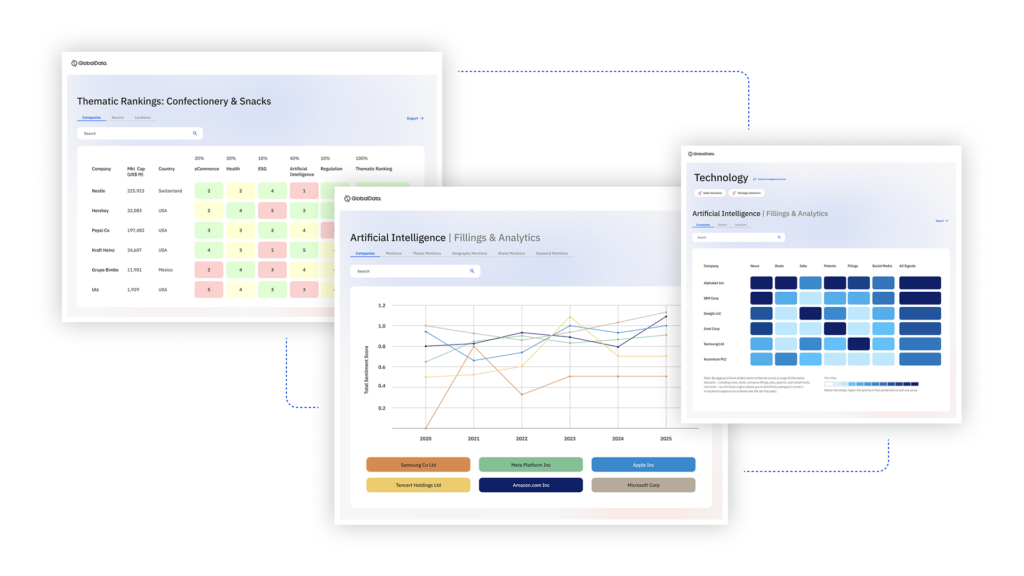
US Tariffs are shifting - will you react or anticipate?
Don’t let policy changes catch you off guard. Stay proactive with real-time data and expert analysis.
By GlobalDataThis helps ensure that the final product’s colours are accurate and consistent across the entire production batch
Why are they necessary?
Colour consistency is critical in branding. Think of iconic food brands—many of them rely on specific colours to be instantly recognisable on the shelves. Any deviation in these colours could lead to consumer confusion or harm the brand’s image.
The role of process control patches is to prevent such inconsistencies by ensuring that the packaging stays true to the brand’s original colour specifications.
These patches are especially useful in large-scale packaging production. If a machine begins to print colours inaccurately, the patches make it easier for technicians to diagnose and adjust the settings, thereby minimising waste and maintaining high print standards
The origins of colour blocks
The use of colour blocks in packaging comes from the print industry, where quality control has always been essential. The CMYK colour model, standard in printing, was introduced to make it easier to mix and reproduce various colours using just four basic inks.
As printing technology advanced, the need to ensure precise colour reproduction became even more important, especially as brands grew and their packaging was printed across multiple locations.
This technology is not unique to the food industry; it is widely used across all sectors that require large-scale printing, from consumer goods to cosmetics packaging
Who uses them and why?
Process control patches are used primarily by printers and packaging manufacturers. These companies print millions of units, so they need a reliable way to monitor quality. The colour blocks help technicians adjust the printer settings in real time to avoid mistakes.
However, they are also used by packaging designers who want to ensure that their carefully chosen colours are reproduced faithfully during the manufacturing process.
While these colour patches are essential for quality control, they don’t serve any direct purpose for the consumer. However, knowing their function provides an insight into the complexity behind even the simplest-looking food packaging
How useful are they for consumers?
For the average shopper, the colour blocks don’t offer any relevant information about the product itself. They are purely for the printers’ reference and have no bearing on the food’s quality, safety, or nutritional content.
So, consumers can safely ignore them, though they do represent the behind-the-scenes work involved in ensuring the packaging you see in stores is of the highest standard.
However, from an industry perspective, these patches are invaluable. By maintaining consistency and reducing errors, they help packaging companies avoid costly reprints and ensure that consumers are always able to recognise their favourite products on the shelves.
To sum up, while the coloured dots on your food packaging might seem trivial, they play a critical role in maintaining the quality and consistency of the packaging.
Used by manufacturers and printers, these process control patches ensure that the design remains faithful to the original, preventing any colour discrepancies that could confuse consumers or damage brand integrity.
Although they offer no direct benefit to consumers, understanding their purpose adds an interesting layer of insight into the complexity of food packaging production.