
Swiss packaging and label equipment manufacturer BOBST has announced that its SelectMet system has been upgraded to implement its F&K heritage flexo printing technology into the vacuum metalliser.
The integration eliminates the complexity of special lacquers and chemical baths used in the traditional demetallisation processes, making this system a simple and economic alternative.
The BOBST SelectMet process operates at speeds of up to 400m/min on the BOBST General K4000 platform.
The system allows users to benefit from greater flexibility, since one machine can be used for two processes simultaneously, namely standard aluminium metallisation and selective metallisation.
The product has been released with regular metalliser width variants of 1,250mm and 1,650mm.
The flexo printing unit has been installed inside the vacuum chamber for the equipment, so the print head can be moved if needed.
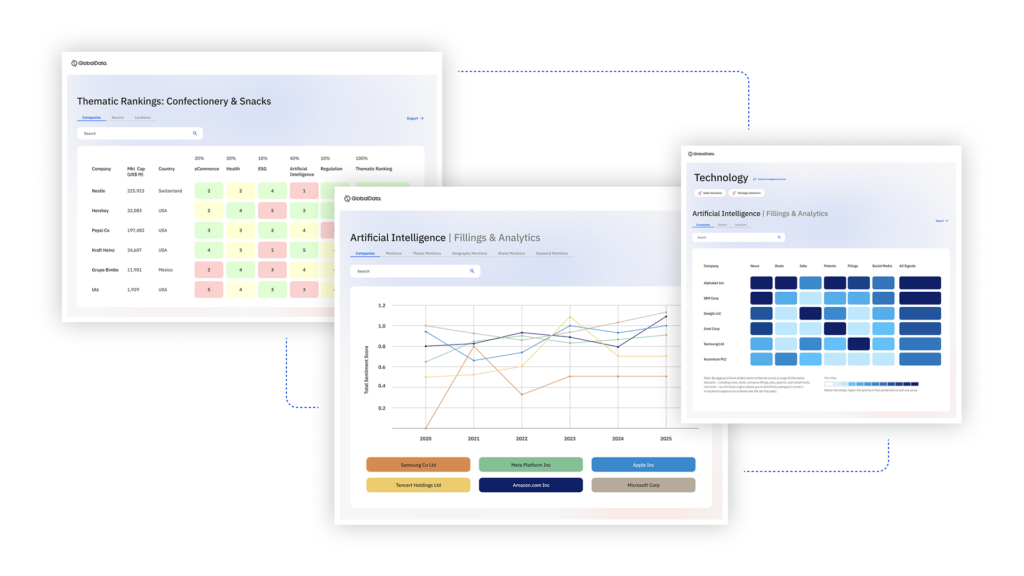
US Tariffs are shifting - will you react or anticipate?
Don’t let policy changes catch you off guard. Stay proactive with real-time data and expert analysis.
By GlobalDataIt has been equipped with a polished Anilox roller and a high-precision Doctor blade made out of carbon fibre, which allows accurate oil metering, BOBST said.
It also enables quick and easy adjustments to the printing sleeve unit.
Image: BOBST SelectMet operates at speeds of up to 400m/min on the BOBST General K4000 platform. Photo: courtesy of BOBST.