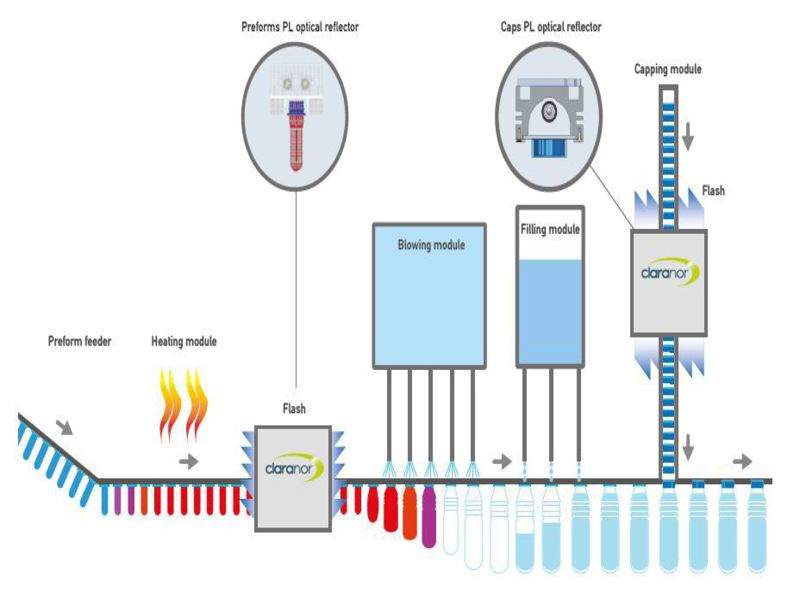

France-based Claranor, in collaboration with blow-moulding machine manufacturer 1Blow, has developed a method to achieve a chemical-free production line through polyethylene terephthalate (PET) preform sterilisation.
In order to develop the process, both companies have conducted a series of microbial tests to demonstrate a high killing rate on preforms.
PET ultra-clean-filling lines, which use hydrogen peroxide (H2O2) for packaging decontamination, are currently used in the juice, soft drink and bottled water markets.
Claranor has inoculated 0.5l transparent preforms with Aspergillus brasiliensis and evaluated the resulting decontamination obtained in the oven of a blow-moulding machine.
Decontamination was determined using a combination of oven heat and the company's pulse light sterilisation technology.
Claranor noted that when combined with Aspergillus brasiliensis, PET ultra-clean-filling lines are unaffected by heat, but the pulse light displayed positive results.
According to Claranor, the newly developed process can be used for industrialisation, since the pulsed light reflector can continuously and distantly treat preforms passing from the oven to the blowing machine.
The new process has paved the way for chemical-free ultra-clean lines, which can be equipped with Claranor Puls’Combi PET preform and cap sterilisation with pulsed light.
In 2010, Claranor launched its pulsed light technology for the beverage and dairy industry, enabling cost-effective surface sterilisation without chemicals.
Image: Claranor Puls’Combi PET. Photo: courtesy of Claranor.