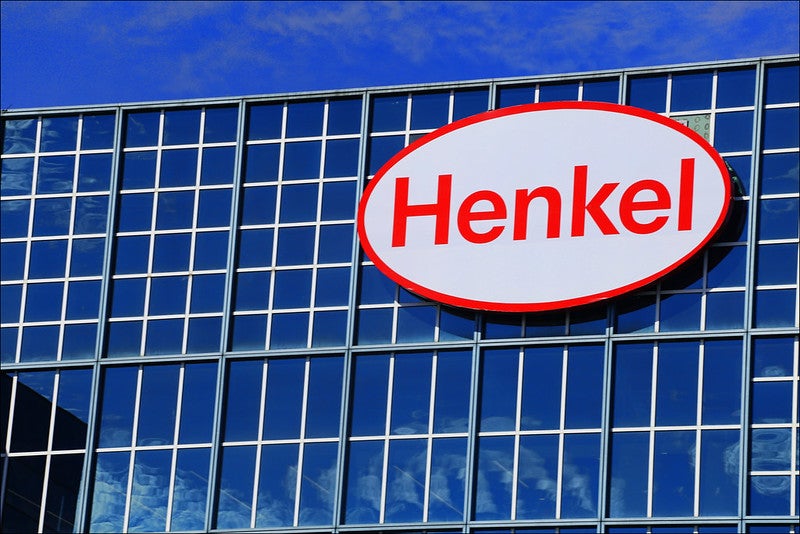
Germany-based consumer goods company Henkel has invested in a stretch-blow moulder from filling and packaging firm KHS, featuring preferential heating capabilities, in an effort to increase its polyethylene terephthalate (PET) bottle production.
The company has installed the blow moulder at its site in Wassertrüdingen, Germany.
Henkel will use the technology for its Fa body care brand, its first investment in a stretch blow moulder for the beauty segment.
The KHS system has the capacity to process up to 21,700 bottles an hour.
Henkel has also worked with KHS to reduce the material use of its 250mm bottle by 14% through KHS’ Bottles and Shapes container design consultancy programme.
The bottles are made entirely from recycled PET, 25% of which is so-called ‘social plastic’ collected in partnership with the Plastic Bank social enterprise.
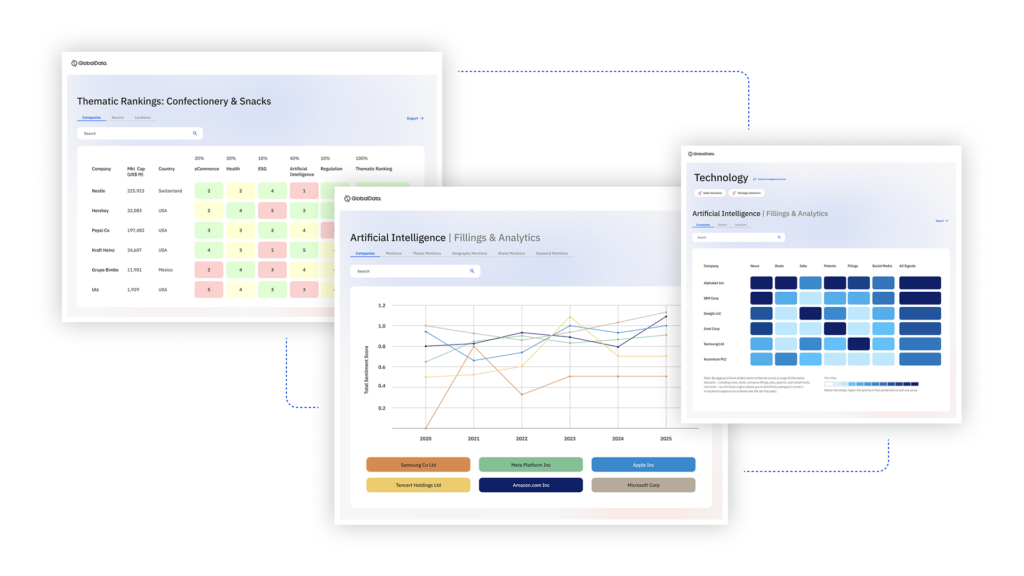
US Tariffs are shifting - will you react or anticipate?
Don’t let policy changes catch you off guard. Stay proactive with real-time data and expert analysis.
By GlobalDataHenkel Wassertrüdingen site managing director Christian Bauer said: “We’re planning on also increasing this percentage in other containers in the future in order to make our entire portfolio even more eco-friendly.”
KHS global product account manager Björn von Lengerke said: “You can make the respective containers for the various products yourself. This makes production plans more flexible.
“In the preferential heating method, preforms are first heated in the heater as they rotate.
“In the downstream section, rotation is then stopped, so that only certain areas of the PET preforms are heated further.”
The system also features a heater box designed to transfer the required heating energy through opposite heater levels.
Von Lengerke said that this ‘optimises the material distribution and stability of the bottle’.
Henkel Beauty Care executive Claus Meyer said: “With this measure, we’re consistently aiming to further reduce our ecological footprint throughout our value chain.”
Henkel has committed to making all its packaging recyclable or reusable by 2025.
In October last year, the company partnered with Austria-based packaging and recycling company ALPLA to develop recyclable packaging for its Somat dishwashing gel products.