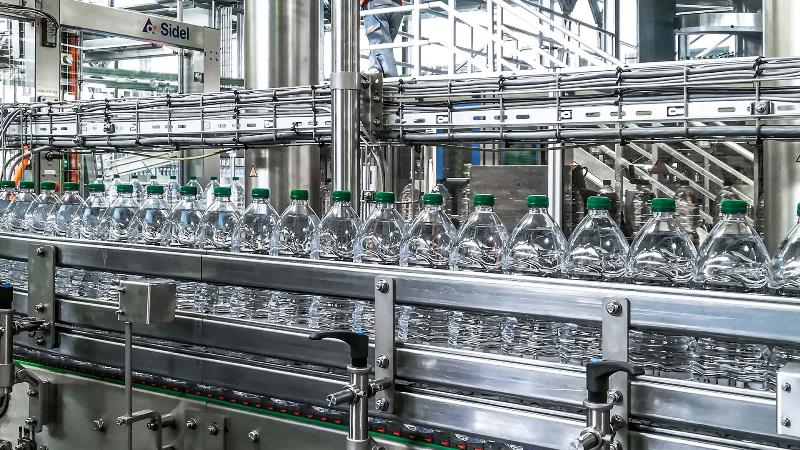
Italian bottled water brand Levissima has installed EvoDECO Roll-Fed from Sidel to enhance its label application and increase the output capacity.
The partnership with Sidel has allowed the company to address the demand in the country for its re-designed 1.5l Alpine bottled water produced through a new complete line.
The re-designed 1.5l bottle now features a shorter neck but continues the brand’s square shape. It is produced with an output speed of more than 46,000 bottles per hour (bph).
Levissima Plant Manager Franco Simoncini said: “We were familiar with the high quality and hygienic standards provided by the Sidel equipment.
“The competences and the customer-centric approach shown by their team during the commissioning and the installation phases, together with smooth project management were helping further to reconfirm our trust in the company.”
According to Sidel, EvoDECO Roll-Fed labeller with two stations was installed to match the output speed for the production of the squared 1.5l bottle, as well as handling lightweight containers and ultra-thin labels.
The labelling machine also features a system installed on the vacuum drum to perform cleaning and maintenance operations such as removing glue residuals.
The machine is also fitted with an automatic label extraction system to ensure all bottles are properly labelled, a vertical melter and the laser-engraved glue roller to melt glue on demand and circulate it at a precise temperature.
Levissima has also installed Sidel Matrix Combi combined with a Sidel SF100 no contact filler to increase performance and production capacity and ensure optimum uptime at the company’s Cepina facility.
Combi integrates blow moulding, filling and capping processes into a single system to assist companies in reducing operating costs.