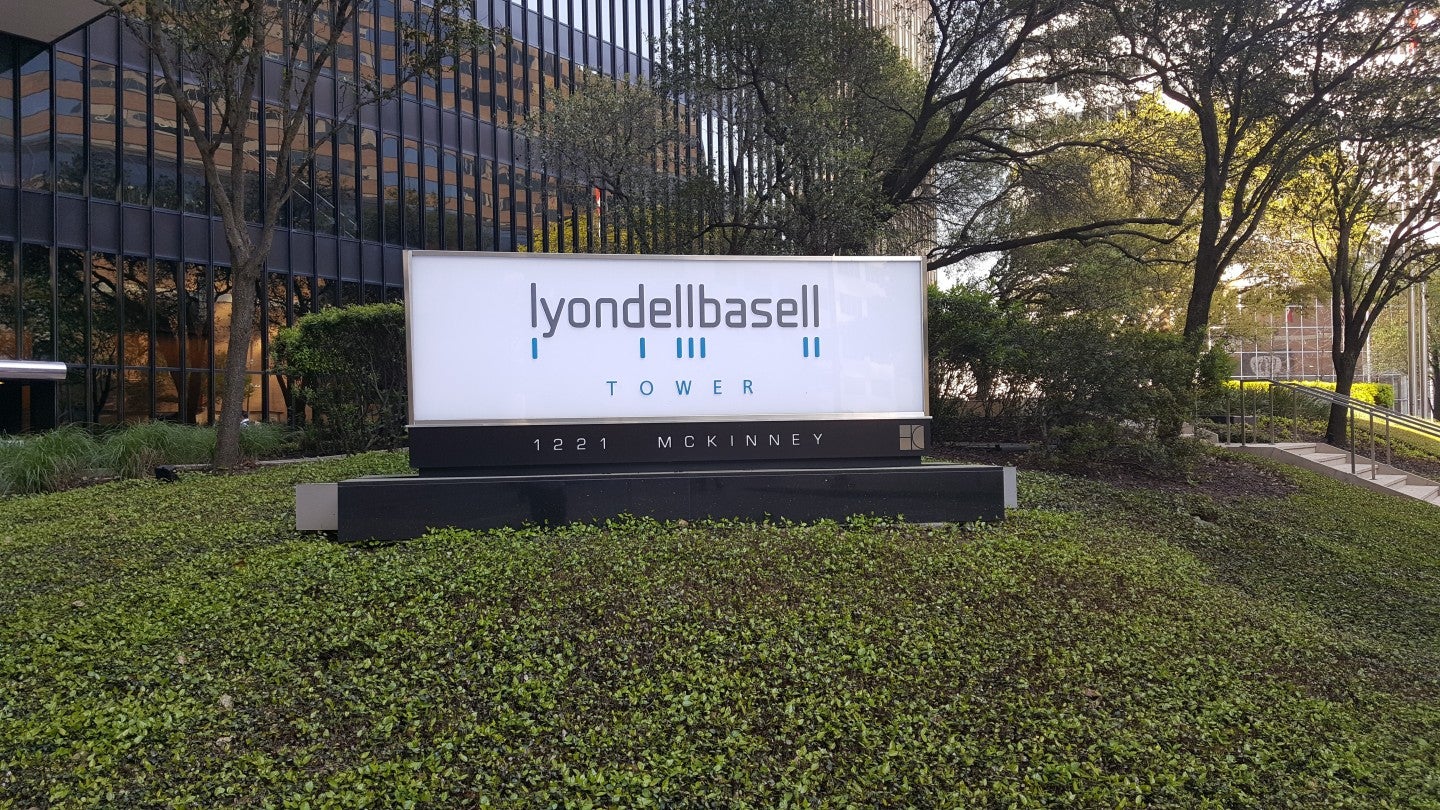
LyondellBasell has taken the final investment decision to establish its first industrial-scale catalytic advanced plastic recycling demonstration plant in Germany.
The new facility will be located at LyondellBasell’s Wesseling site in the country.
It will be the company’s first single-train recycling plant that will convert post-consumer plastic waste into feedstock to produce new plastic material.
This conversion process will leverage LyondellBasell’s proprietary MoReTec technology, which produces both pyrolysis oil and pyrolysis gas.
Some benefits offered by MoReTec technology include lower energy demand and electrical heating via net-zero greenhouse gas emissions.
Pyrolysis oil serves as a sustainable alternative to fossil-based materials in polymer production while pyrolysis gas recovered through MoReTec technology replaces fossil-based feedstocks.
The polymers produced using recycled feedstock from the new facility will be sold by LyondellBasell under its ‘CirculenRevive’ product line.
It will be used for various medical and food packaging applications.
The majority of the sorted processed feedstock will be supplied by Source One Plastics, which is LyondellBasell’s joint venture partner with 23 Oaks Investments formed in October last year.
LyondellBasell CEO Peter Vanacker said: “We are committed to addressing the global challenge of plastic waste and advancing a circular economy, and today’s announcement is another meaningful step in that direction.
“Scaling up our catalytic advanced recycling technology will allow us to return larger volumes of plastic waste back into the value chain.
“By doing this, we will have the ability to produce more materials for high-quality applications, retaining value of plastics for as long as possible.”
Construction of the new factory is expected to be completed by the end of 2025.
Once open, it will have the capacity to recycle up to 50,000 tonnes (t) of plastic waste annually.
It will also address the issue of recycling hard-to-recycle plastics such as mixed/flexible materials, which are typically sent to landfills if they can’t be recycled.
The latest investment decision builds on the company’s initial announcement to proceed with engineering for the development of this facility.