Italian liquid detergent producer Saci has selected UPM Raflatac’s ProLiner PP30 for some of its product labelling.
ProLiner is a film release liner that allows a uniform adhesive profile, increasing frontal print capacity and enhancing production efficiency through the reduction of machine downtime related to backing failure.
The fully recyclable polypropylene-based liner is 50% thinner than siliconised paper, which benefits the manufacturing process.
Saci CEO Filippo Campanile said the material addresses the company’s sustainability requirements and has also enabled the company to transform a disposal cost into a source of revenue.
For the same spool diameter, the material holds about 20% more labels with a consequent saving on storage space, transport costs and machine downtime for spool replacement.
According to Saci partner Etiservice Pomezia, a Roman company specialised in the production of self-adhesive labels and coupons, the material also requires less tension on-press.
How well do you really know your competitors?
Access the most comprehensive Company Profiles on the market, powered by GlobalData. Save hours of research. Gain competitive edge.
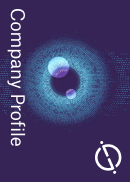
Thank you!
Your download email will arrive shortly
Not ready to buy yet? Download a free sample
We are confident about the unique quality of our Company Profiles. However, we want you to make the most beneficial decision for your business, so we offer a free sample that you can download by submitting the below form
By GlobalDataWhen added to the ability to use a spool length of 6000m, this translates into a productivity increase of 10%, claimed the company.
The firm believes that ProLiner PP30 works as an alternative to traditional glassine liners and offers the combination of lower total applied cost and recyclability.
The material contains no fibres, which indicates that in terms of print quality it is cleaner on press than any paper liner.
Through UPM Raflatac Italy, Saci teamed up with a local recycler Ecoplast, who supply the company with containers for collecting the used ProLiner and also pay a fee for every tonne collected, as the polypropylene can also be processed and turned into new products.