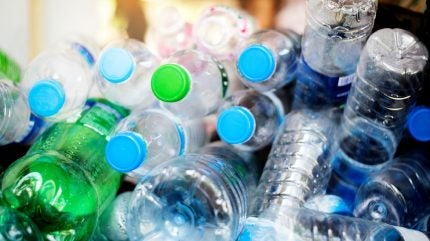
Industrial technology company Schneider Electric has partnered with polyethylene terephthalate (PET) chemical recycler GR3N to cater to the advanced plastic recycling industry with an open automation system.
This collaboration aims to address the challenges of PET waste by deploying GR3N’s Microwave Assisted DEpolymerization (MADE) solution.
The technology breaks down PET into its chemical building blocks that can be integrated to develop new PET pellets for packaging and textiles.
GR3N’s MADE solution, based on alkaline hydrolysis, can handle a higher amount of impurities than current technologies.
Earlier this year, GR3N demonstrated the technology and Schneider Electric’s open automation technology, EcoStruxure Automation Expert, at its demonstration site in Italy.
The pending MADE plant is designed to integrate all the technologies that will be adopted in the venture’s first industrial-scale facility, anticipated to be established in Spain.
This facility is expected to handle more than 40,000 tons per year of PET waste.
The partnership, which began with a memorandum of understanding, will enable GR3N to scale its operations to new sites in a quick and cost-effective manner.
The solution is projected to achieve industrial scale by 2027 with the establishment of a 35-40 kilotonnes per annum plant, incorporating pretreatment, depolymerisation, and repolymerisation processes.
GR3N head for marketing and business development Fabio Silvestri said: “Through software-defined automation and hardware independence, we have been able to effectively derisk our operations and push the boundaries of our technology.
“We’ve been able to reconfigure our systems quickly when we see opportunities to improve efficiency, while avoiding supply chain issues due [to] the hardware-agnostic nature of the system. This is what is needed to make advanced plastic recycling at reality at scale.”