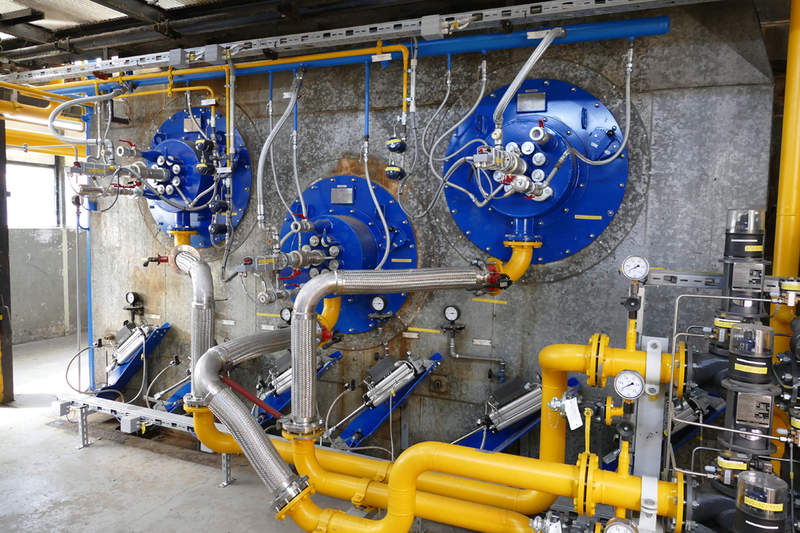
German speciality papers and carton board manufacturer Zanders is investing in the conversion of the on-site power plant from hard coal to natural gas at its Bergisch Gladbach location, as part of its investment programme for sustainable increases in efficiency.
Through the conversion, the company aims to enhance efficiency in the production processes of the paper mill.
Similar to a gas grill, which heats and cools down much faster when compared with a coal grill, a gas-fired power plant can allow rapid changes of load.
The conversion, which is expected to increase the service life of the systems, will allow the company to transform starting and stopping the paper machines into more flexible and efficient processes.
Zanders power plant manager Ralf Wenz said: “The conversion of two boilers in our power plant has mostly been completed.
“The gas has been flowing since the end of July and the commissioning of the first boiler is expected to be completed by the end of August, so that we will probably no longer need coal for the steam supply of our plant during normal operation by the end of September.
“We are now preparing the conversion of the third boiler, which will take about a year. By that time, both main boilers and the reserve boiler, and thus the entire power plant, will be converted to gas.”
According to the company, the power plant conversion will eliminate the cost of disposal of the ash associated with the previous coal-fired operation.
Zanders also expects to achieve a reduction of more than 40% in CO2 emissions.
The company is expected to spend around €7m towards the modernisation of the plant.
Other steps at the plant include the installation of new LED lighting throughout the plant, as well as the insulation of the steam pipes and the optimisation of the compressed air system.