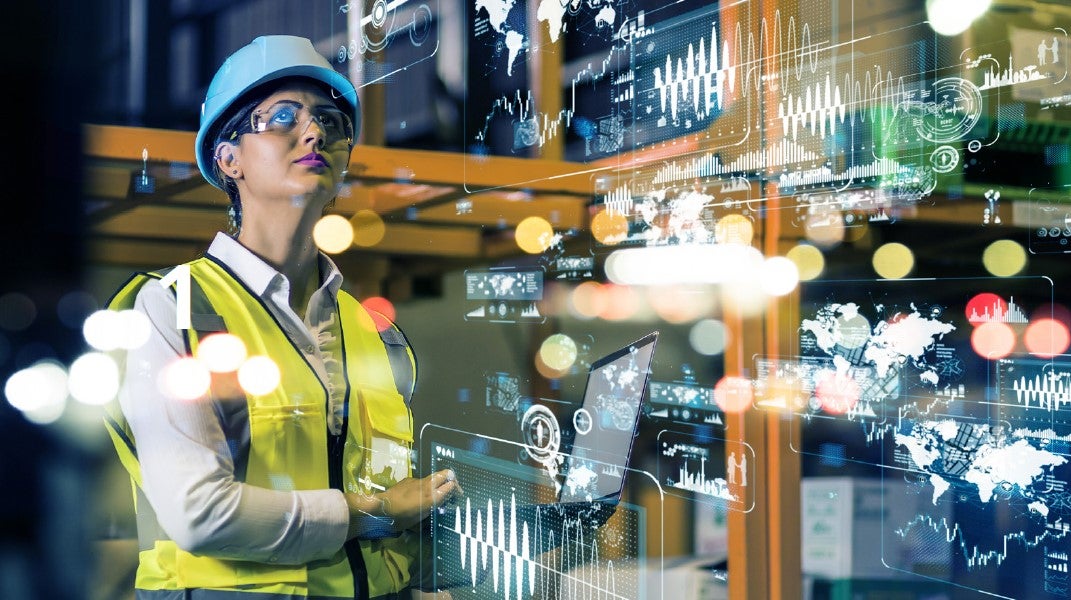
The smart factory offers a more integrated and interconnected system that makes available a continuous flow of data for connected performance and production. For this to work, there needs to be horizontal integration and vertical integration into the organisation’s operational systems and the whole value chain.
SICK’s Consulting and Digital Solutions team works with customers so that their digital transformation can be completed easily and smoothly. The company’s solutions comprise smart sensor applications that connect the shop floor and the data floor.
Several benefits of digital transformation technology include addressing the labour gap challenge by reducing waiting time, simplifying the workers’ series of tasks, and expediting operations. Humans and technology work together to boost productivity, speed-up processes and minimising the risk of injury during work.
Another advantage is addressing inventory challenges, which normally lead to high costs. By reducing the extra stock supply and inaccurate stock numbers, SICK’s solutions guarantee precision of demand planning and help prevent overproduction and minimises cost. With the help of intelligent camera solutions, supply is monitored correctly.
In addition to accuracy of supply, quality monitoring is also ensured. With SICK’s technology, quality problems are solved as the manufacturing process is better organised, and the procedures of packaging, distribution and installation are enhanced. Statistical process control (SPC), advanced process control (APC) and digital performance management ensure that there is a supply and demand match which increases value potential.
Additional benefits of SICK’s technology include improved resources and performance, as well as speeding up the development process, which leads to the products entering the market at a reduced time. This, in turn, leads to reaping the advantaging of entering the market early through increased revenue and innovation. Further potential is added by decreasing the cost of service which relates to maintenance and repair, thus increasing value potential, as well as boosting asset utilisation by decreasing downtime.
Five-step process for digital transformation with SICK
This five-step digital transformation process starts with an initial assessment of existing conditions and infrastructure when it comes to the client’s facilities. This enables the development of a customised solution that perfectly fits the client’s needs and addresses existing challenges. Understanding the objectives for each client’s business is key for providing the best possible service.
Upon the completion of the assessment, a solution concept is created to meet customised business objectives. Some examples of this are risk and compliance tasks that need to be addressed, as well as track-and-trace solutions that relate to operational projects. A design then is made to put the assessment and the solution concept to practice.
Solution design is related to a variety of different applications that include:
- Sensor-up (Edge-to-Cloud): bringing data to the data floor on servers and
Cloud platforms
• Data-down (Cloud-to-Edge): utilising sensor data to optimise business performance
• A combination of the two
Another step in the five-level digital transformation process is implementing a data concentrator methodology into existing platforms and create a seamless connected experience where data is sent to the Cloud and can be easily accessed. The data might include information about machine status, temperature, pressure values, etc. In this way, production processes are simplified and optimised at the same time.
The last step comprises verification and validation. The SICK team partners with the clients for excellent and timely customer service every step of the way. The team ensures that everything is working seamlessly throughout the whole process, from conception to design and installation. Data gathering is at the centre of SICK solutions so that efficiency and top quality are guaranteed.
According to Thomas Warburton managing director Marilena Romano: “At Thomas Warburton, we manufacture business value by offering Industry 4.0 solutions for our customers’ C-Part Inventory Management. We continually improve and optimise our internal process as well our customers’ value chain. Industry partners like SICK Sensors support us to develop digital transformation solutions through a consultative and agile approach.”
Pallet audit system case study
SICK helps clients find solutions to challenges. An example includes a supplier who was having trouble with stock being delivered to the wrong retail stores or delivered in the wrong quantities. Prior to using SICK’s solutions, the operations were completed manually, and therefore the production and distribution process was prone to have some mistakes.
To this end, and after a recommendation of SICK to the client by a retailer, SICK offered a track-and-trace solution called Pallet Audit System by which the client could use SICK’s ICR camera tunnel system to ensure the correct quantity and location are selected. The high-resolution image quality that the camera produces renders accurate read rates to boost sorting processes. The solution also increases throughput to more than 18,000 objects per hour. Data reading and processing is therefore pivotal in the way SICK solves these challenges and provides automated solutions that boost production and sorting operations.