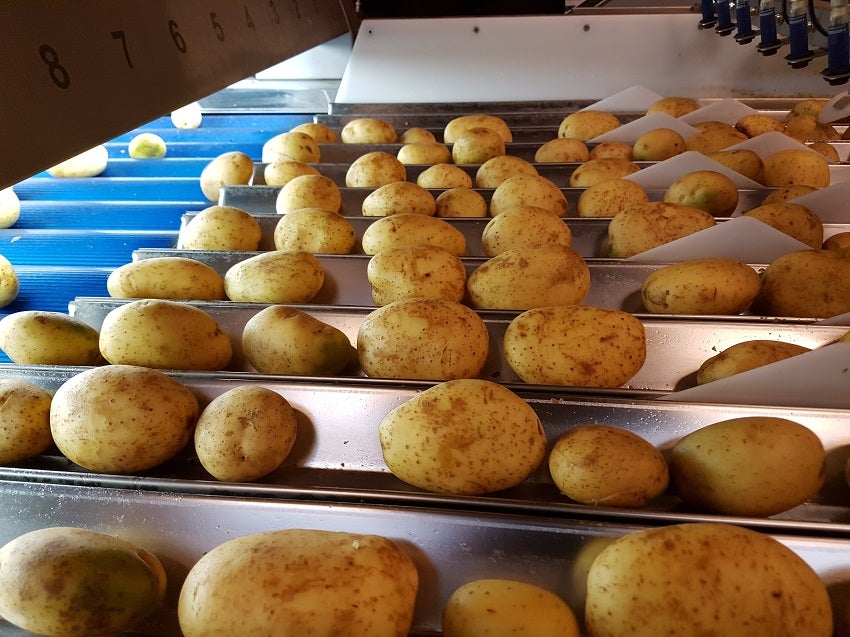
Newtec provides a portfolio of highly innovative solutions for potato sorting and visual inspection, deploying technology such as cameras that inspect products during processing to eliminate any spoiled items.
What are your company’s latest innovations in potato sorting equipment?
Firstly, there is the cost-benefit determination of a given potato batch.
We have been developing algorithms for analysing and to determine the optimal way to split a given batch towards the customers’ needs and requirements.
In other words, automating the process of setting up the sorting on quality and sizing, based on the given raw material versus orders to be delivered.
These new features remove the responsibility expert operators have in setting up the parameters on the sorting machines.
Having the machine doing the parameter adjustments instead, based on true and large statistical insight, secures a much better chance of fitting the given potato batches into product-groups based on the current business values.
How do you see the market for such equipment evolving in the near to mid-term future?
We believe that enhanced communication within the assembly line will better address the near-term requirements of the production installations.
The value of sharing information between various functionalities will be essential in achieving a fully automated and modular production environment, whether this will occur through ‘Industry 4.0’ or any other IoT standard.
With sorting, we see a clear trend towards increasing the number of sorting outlets.
Having the ability to bring out special selections and divide the bulk product into more groups, and thus increasing the uniformity, raises the potential value that can be added to the raw material in the production.
Can you explain how Newtec’s latest technology aids potato verification?
By introducing our latest version of the Qtechnology UHD camera, along with a new in-house developed LED-light system, we do feel that we have met most of the challenges relating to size-grading, as well as external evaluation and examination of the potatoes – at least for the time being. We still have numerous ideas for future developments.
As an example, we are ready to add more intelligence into the machine, and thereby, within limits, let the machine adjust itself by referring to orders that need to be packed. By allowing this, we estimate significant savings in both raw materials and time to reach grading targets. By doing this, we can move the decision-making away from the shop-floor and turn it into an automated process and thereby ensuring the packer the highest value in each batch of potatoes.
Furthermore, by installing a Newtec-developed software system called WebServices, the Celox customers can collect all data from the products passing through the grader. This system is very flexible and allow the users to enter a large variety of information and thereby ensure full traceability. WebServices is available in numerous different languages and can be set up to individual needs, according to the desired information.
By using WebServices, the customers will automatically be informed on the status of the Celox machines, as well as the status of the potatoes being graded.
We do see an increasing need for our customers to collect the production data, both to optimise their own operation, but also for documentation towards their customers.
What are some of the international trends for optical graders?
Today, most of the optical graders are sold and installed in Europe and North America, a fair number has gone to Australia and we see China moving fast in this direction as well.
Again, as mentioned earlier; this technology brings so much more than only labour savings. We see large multi-international potato processing companies investing in this to optimise the potatoes towards their final products, we see customers installing the machines to secure the consistency in quality towards the supermarkets, and we see customers using the machines to make special selections for campaigns and thereby optimising earnings.
All over the world, the potato industry is a highly competitive segment to be part of. Every day farmers and packers work with low margins and it is crucial to both get the volumes, but also to ensure the highest earning of every single potato, and that is exactly what the Celox optical grader is made for.
What are the key considerations when choosing an optical grader solution?
When looking for or choosing an optical grader the outcome is, of course, the first thing to ensure. Can the machine do what is needed, and does it do with the accuracy needed? This goes for both size and quality.
It is crucial to establish that a machine is able to handle and detect defected items during production, as well as be adaptable to detect new or unfamiliar faults.
Newtec machines offer a consistent flow of potatoes through the machine, which makes sure that the energy used is constant and not prone to fluctuations.
In addition, it is important to monitor and certify the machine’s product handling process. For instance, when handling potatoes, the equipment is designed to maintain a consistent production flow with minimal drop heights to retain the quality of the product. This ensures that no return system is required while enhancing product handling capabilities.
The machine’s performance should be consistent in quality in terms of grading and design, ensuring that no systems are returned with defects. This means that more products can be handled and there are production downtime is kept to a minimum.
Last but not least; today space is money.
As a customer, the footprint of any machine is important. With regards to optical graders, there will always be a certain amount of equipment before and after, so the physical size of the grader itself is important in most cases. The customer can ask the question; ‘how much space is needed to run my production?’