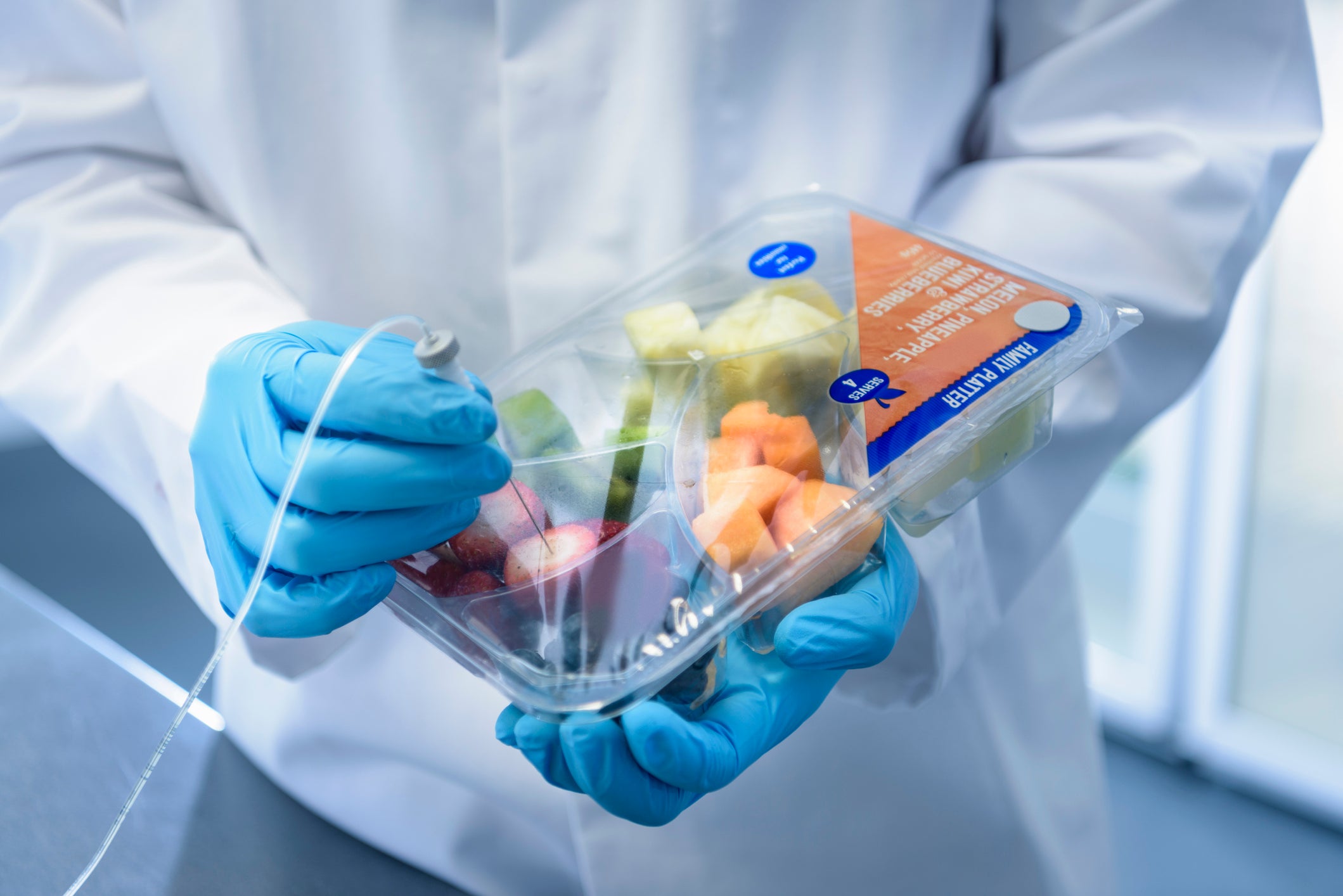
A recent study conducted by the Packaging Machinery Manufacturers Institute (PMMI) and Interact Analysis has shed light on the packaging industry’s interest and needs for Condition Monitoring and Predictive Maintenance.
Based on customer feedback, the study has uncovered valuable insights regarding pain points in the packaging process, the machines and components that require monitoring, the data that should be gathered, current maintenance approaches and the potential for a more efficient solution.
What keeps customers awake at night?
The survey conducted by PMMI reveals that form, fill & seal machines, filling & dosing machines and labelling machines are of the utmost importance in packaging processes and are more likely to experience failures compared to other machines.
These three categories of machines are critical components in the production line, particularly in primary packaging.
How well do you really know your competitors?
Access the most comprehensive Company Profiles on the market, powered by GlobalData. Save hours of research. Gain competitive edge.
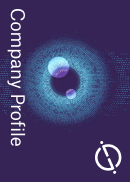
Thank you!
Your download email will arrive shortly
Not ready to buy yet? Download a free sample
We are confident about the unique quality of our Company Profiles. However, we want you to make the most beneficial decision for your business, so we offer a free sample that you can download by submitting the below form
By GlobalDataDownstream processes are generally less critical. Given their high-speed operation and handling of perishable products, any downtime experienced by these machines can significantly impact overall equipment effectiveness (OEE), quality and profitability.
See Also:
The components on these machines that are most likely to fail include pneumatic systems, gearboxes, motors/drives and sensors.
How can customers reduce unplanned downtime and improve OEE?
According to the data obtained, the top concern for customers is unplanned machine breakdowns.
However, many packaging firms still rely on reactive or preventative maintenance approaches, which may not effectively address the majority of failures.
An ARC study reveals that only approximately 20% of failures are age-related while the remaining 80% are non-age-related and likely not addressed by traditional maintenance programmes.
A more effective approach to mitigating potential failures is to implement condition monitoring for critical machines and components. Monitoring their condition makes it possible to detect early signs of deterioration or impending failure, enabling predictive maintenance.”
Smart sensors now have the capability to measure various attributes such as vibration, temperature, humidity, pressure, flow and inclination. This data can be used to alert users of emerging problems.
Some of these sensors can also self-monitor and notify users of potential failures within the sensors themselves.
What are packaging customers actually doing?
Encouragingly, the packaging industry is actively pursuing a better way to address these challenges.
A quarter of customers have already implemented some form of Condition Monitoring/Predictive Maintenance, with an additional 20% currently piloting these methods and 30% planning to implement them.
This demonstrates a high level of interest in Condition Monitoring/Predictive Maintenance, surpassing the interest in any other technology discussed in the PMMI survey.
Where do you start?
To embark on the path towards improved maintenance practices, it is advisable to identify the machines that cause the most frustration.
PMMI has identified form, fill & seal, filling & dosing and labelling machines as critical ones, but there are other machines like bottling, cartoning and case/tray handling machines that could also cause production downtime or damaged products.
Consider the potential failure points and modes of equipment within your own experience or consult with partners or equipment suppliers who use similar machines.
Analyse the components of the machines that are most likely to fail, focusing on moving parts such as motors, gearboxes, fans, pumps, bearings, conveyors and shafts.
Determine the key parameters to measure for each machine. Vibration is a common parameter, often assessed in conjunction with temperature and humidity. Pressure, flow, or amperage/voltage may need to be measured on certain machines.
Finally, assess the most appropriate maintenance programme for each machine. Evaluate the costs and benefits of reactive, preventative, condition-based monitoring, or predictive maintenance approaches.
In some cases, allowing a non-critical, low-value asset to “run-to-failure” may be acceptable while critical machines may warrant investment in Condition Monitoring or Predictive Maintenance to prevent costly failures.
It is recommended to start small by implementing condition monitoring on one or two machines and then scale up once valuable lessons have been learned. Utilising low-cost sensors that can be easily integrated into existing control architectures or added externally is an excellent way to commence the journey.
Condition Monitoring and Predictive Maintenance present packaging firms with a “better way” to address critical concerns such as machine downtime, failures and OEE.
By monitoring attributes such as vibration and temperature on critical machines and analysing the data, users can shift from reactive to proactive maintenance approaches.
This proactive approach allows for the detection and prediction of potential failures before they become critical, thereby reducing unplanned downtime, improving OEE and saving money in the process.