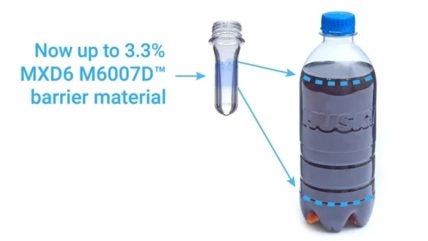
Husky Injection Molding Systems, in collaboration with Mitsubishi Gas Chemical, has significantly improved its multilayer polyethylene terephthalate (PET) solution for small-format carbonated soft drink (CSD) packaging.
This advancement, recognised by the American Association of Plastic Recyclers (APR) for incorporating up to 3.3% MXD6, expands the potential for sustainable and recyclable packaging solutions in the beverage industry.
Addressing challenges in small-format CSD packaging
While PET reigns supreme for larger CSD bottles (356-600ml) due to its strength, clarity, and eco-friendliness, smaller formats (355ml and below) pose a challenge. PET’s permeability allows carbon dioxide (CO₂) to escape, reducing shelf life.
Traditionally, thicker and heavier monolayer bottles were used to address this, impacting both cost and sustainability. Alternatively, adding nylon for better CO₂ barrier properties disrupts the PET recycling process.
Aluminium cans, often preferred for smaller sizes, have limitations such as resource scarcity, higher material costs, and a larger carbon footprint compared to PET.
Husky’s multilayer solution
Husky’s innovative multilayer package offers a solution that prioritises both performance and sustainability.
This technology leverages Mitsubishi Gas Chemical’s M6000 series barrier material, offering:
Enhanced CO₂ retention: Engineered for superior CO₂ control, good mechanical performance, and easy separation from PET during recycling.
Precise injection: Optimises MXD6 usage for maximum barrier effectiveness while maintaining a lightweight design.
Full recyclability: Aligns with sustainability goals by remaining fully recyclable through conventional methods.
Cost-effective lightweighting: Reduces PET resin usage, leading to significant cost savings without compromising performance.
Husky’s multilayer equipment: precision and efficiency
Husky’s technology utilises a high-precision coinjection process, sandwiching a functional layer between two PET layers.
This allows for precise control over material amount, thickness, and placement, offering versatility in design.
The HyPET HPP5e family of coinjection systems underpins this technology, maximising production output while minimising part variation and enhancing quality.
Husky’s multilayer solution, recognised by the APR for its improved recyclability, paves the way for a more sustainable future in small-format CSD packaging.
It offers beverage producers a solution that balances performance, cost-effectiveness, and environmental responsibility.