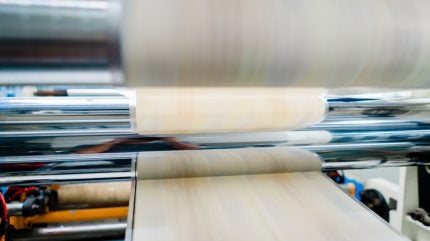
In an era where packaging serves as both a protective layer and a critical marketing tool, the demands on package printing have never been higher.
From vivid graphics and intricate designs to eco-friendly materials and inks, the industry requires equipment that can deliver superior performance consistently. This shift has led to an increase in demand for advanced printing technologies and materials that can deliver exceptional results while minimising waste and reducing environmental impact.
A range of print innovations were on show at Drupa 2024, the premier global trade fair for printing technologies, which took place from May 28 to June 7 in Düsseldorf, Germany. The focus for this year’s event, the first in-person since 2016 as a result of Covid-19 disruption, was digital, sustainability, and new packaging print technology.
Precision strip steel firm Alleima were present, taking the opportunity to highlight its doctor blade steel portfolio, including its latest innovation, Alleima Print XP, a high-end steel grade specifically engineered for long print runs and abrasive inks.
“It was fantastic to be back at Drupa, meeting with our market and the industry, sharing information and getting insights on how print packaging is evolving,” says Senad Kovac, product specialist at Alleima.
“At Drupa 2024, we talked about the shift towards water-based inks over the past 10 years. There was discussion about a new type of ink, PU ink, especially in Europe, as there’s a government demand to switch to these more sustainable options.
“It is of great importance for Alleima to understand the impact of these process changes in order to support our customers with the right material solution for their printing doctor blades”
The role of doctor blades in flexographic and rotogravure printing
Doctor blades are an essential component in flexographic and rotogravure printing processes as they regulate the amount of ink transferred to the substrate, ensuring precision and consistency. As printing technologies evolve, so do the requirements for these blades. High-speed presses and sophisticated designs demand doctor blades that can maintain performance under stringent conditions, including high pressure and varying ink viscosities.
Coatings can be applied to improve properties of the doctor blade. According to Kovac, the most commonly requested coating is a ceramic coating, which improves the durability of the blade but can also contribute to more uniform ink application, reduced friction between the doctor blade and the roller, and protect the blade steel from corrosion. Durability or life length of the blades and therewith uptime for the printing companies is one key feature that customers are increasingly requesting.
“Both flexo and rotogravure printing methods have been used in the packaging industry for a long time, but the wear on the blade is a bit higher with flexographic printing. We talked with a customer who developed a new blade with our Alleima Print XP material, and described it as extremely durable,” Kovac adds.
Alleima Print XP is particularly suited for use with abrasive inks, such as white inks which contain titanium dioxide. This grade ensures more than four times greater wear resistance compared to traditional carbon steel doctor blades.
Alleima’s other offerings include Alleima Print EPS, which is made from hardened and tempered martensitic stainless steel that is suitable for all types of inks. It is characterised by excellent wear resistance, good straightness, and corrosion resistance, ensuring long-lasting performance in various printing environments. Alternatively, Print EP is a hardened and tempered carbon steel that is suitable for non-water-based and UV inks. It features very high wear resistance, good straightness, excellent edge finish, and good dimensional tolerances, making it ideal for high-quality print applications.
The future of packaging printing technology
According to Kovac: “We’re starting to see the development of hybrid machines combining flexographic and digital printing.”
These hybrid technologies integrate the strengths of flexographic printing, such as high speed, cost-effectiveness for long runs, and versatility in substrates, with the advantages of digital printing, which include quick turnaround, variable data printing, and reduced setup time.
“Digital printing is the new thing, but it won’t replace traditional technologies in the upcoming ten years,” Kovac states. “Traditional techniques are still needed for high-resolution and speed. Digital printing is good for producing smaller volume series or individualised products. There have been developments in faster, wider machines that can handle different types of printing jobs without changing equipment, and these require durable blades.”
Find out more about Alleima’s durable materials and coatings, and how they can optimise your packaging printing processes in the free whitepaper below.