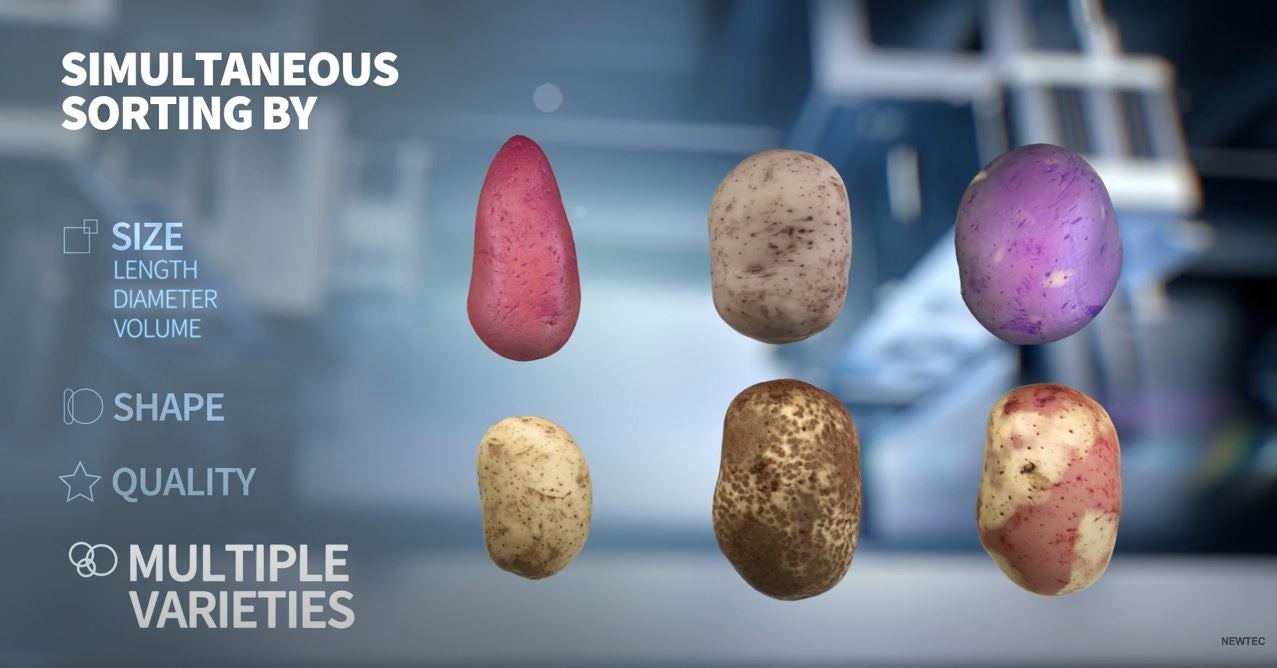
Newtec’s optical sorting machine for potatoes, model Celox-P-UHD, is designed to sort potatoes by size, shape and quality in a single-stage process. The machine sorts washed potatoes directly, eliminating the need for pre-grading and minimising the need for manual labour, whilst ensuring consistent quality output and high throughput.
In a new video, Newtec proudly presents their new and improved camera section of their Celox-P-UHD which includes:
- Newtec AI Vision Engine Gen3
- Dual Lens Cameras
- Next-generation Hardware
“We believe that this is the next generation of optical sorting machines offering countless opportunities”, says head of sales, Christian Max Villadsen.
With a mix of real footage and animations, the video visualises how the highly accurate tracking and grading of the potatoes take place.
Modular design – expandable systems
Up to 16 categories of products can be sorted out simultaneously. Sorting criteria for these categories are instantly customisable according to the current needs. Premium product selections can effortlessly be sorted out of bulk produce. Being completely configurable by the operator or factory manager the sorting machine permits near-instant turn-around time and unparalleled flexibility. Additionally, the machine collects detailed real-time product data which is available with Newtec WebServices. The same data can optionally be integrated into your own business IT systems for further analysis.
Advantages for the customers include:
- Quality, size and shape sorting in one machine
- Accurate selection of high-value products
- Consistent quality output
- No need for mechanical pre-grading
- Gentle product handling
- Robust stainless steel construction
- Modular design for future extension (up to 16 categories/outlets)
- WebServices, our data collection system, enables capturing of complete product information and remote servicing.
Sorting in the most profitable way
Every single potato is assessed in the camera section. The extended camera section is equipped with three cameras that photograph each and every potato up to 45 times to capture precise data on size, shape and surface quality.
The design of our camera sections is adapted to potatoes. The potatoes are conveyed and led through the camera section on vibrating rollers – a unique and patented system which ensures that the potatoes are inspected from all angles because they rotate while they are propelled forward by gentle roller vibrations.
The machine is constructed with maximum efficiency in mind, combining high production throughput with a relatively small footprint.
“We are proud to offer an efficient and space-saving machine that ensures a very thorough quality check and classification of every single crop before it is presented in the sales packaging.
We look forward to optimising the value of each of our customers’ potatoes by sorting them in the most profitable way”, Christian Max Villadsen concludes.
For more, please watch this video.