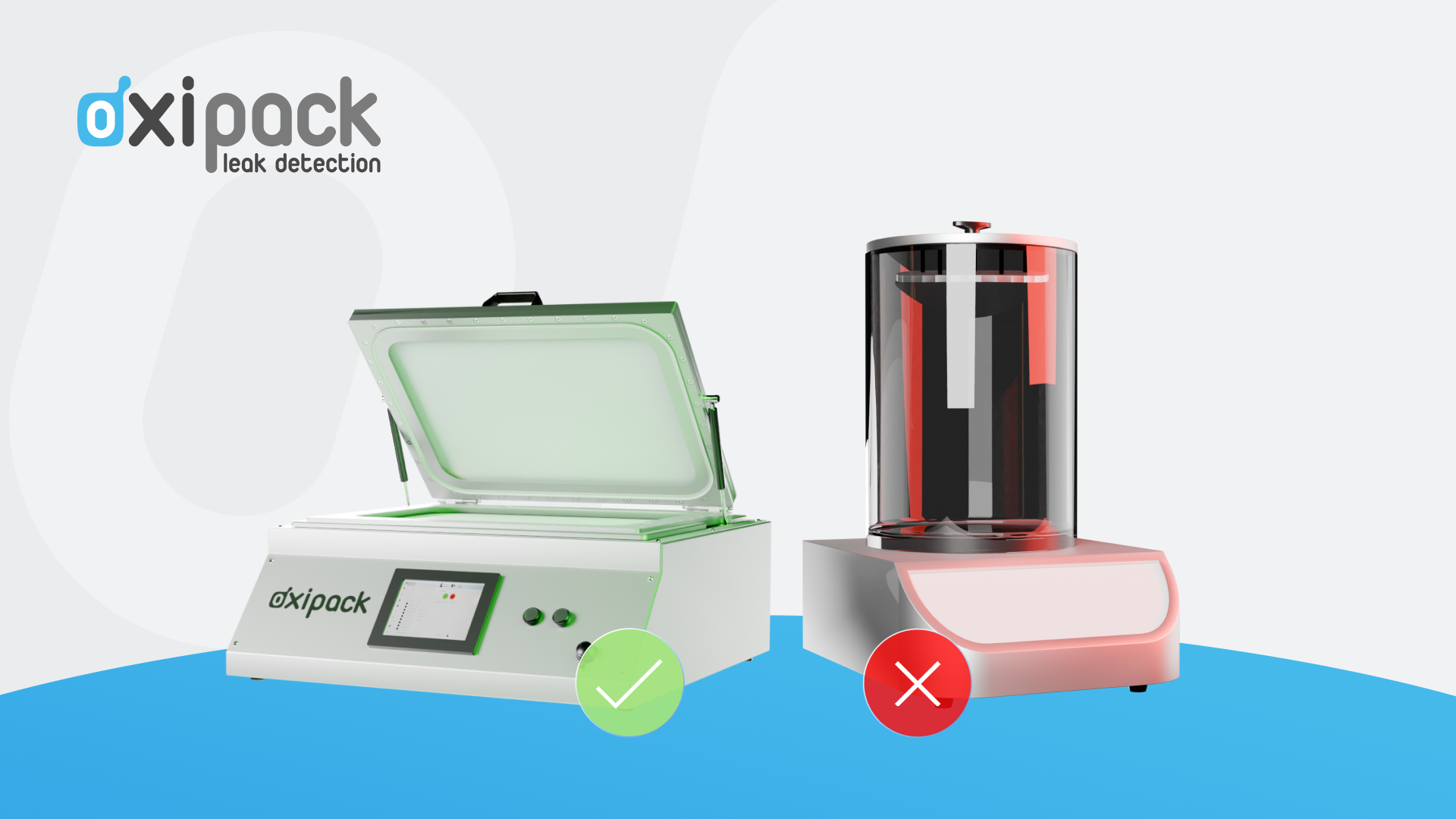
What if the leak detection method your company has relied on for years is actually costing you money and quality? For decades, bubble leak testing has been the norm. But what if there was a better way? Thanks to advancements in vacuum decay testing, industry leaders are making the switch to a more accurate, reliable, and non-destructive approach.
Bubble leak testing, also known as the bubble immersion test, has been a traditional method for detecting leaks in sealed packages. The process involves submerging a package in water and applying a vacuum. If bubbles appear, it indicates a potential leak. While simple in concept, this method is inherently flawed.
First, bubble testing is highly subjective. Operators must visually confirm the presence of bubbles, leading to inconsistencies and potential human error. Second, bubble testing lacks sensitivity. It struggles to detect small but critical leaks that can compromise product safety. Lastly, it is destructive. So, the tested packages must be discarded, creating unnecessary waste and increasing costs for manufacturers.
The importance of vacuum decay testing
The vacuum decay method offers a nondestructive, deterministic alternative that has been recognised by major regulatory bodies, including the FDA and ASTM F2338. Unlike bubble testing, vacuum decay testing does not rely on visual inspection or subjective judgment. Instead, it measures the rate of pressure change in a vacuum chamber, which quantifies leaks with much greater precision.
Vacuum decay testing offers unmatched sensitivity, detecting micro leaks as small as 5 µm. This is far beyond the capabilities of bubble leak testing. Unlike destructive methods that require packages to be discarded, this approach preserves product integrity, reducing waste and allowing for re-testing when needed.
It is also recognised as a deterministic method under USP <1207> for container closure integrity testing (CCIT), ensuring compliance with stringent pharmaceutical and food safety standards. Additionally, vacuum decay testing can be fully automated, eliminating human variability and providing consistent, repeatable results across production lines.
Vacuum decay testing in action
A global food and beverage processing company transitioned from bubble leak testing to vacuum decay testing, significantly improving its packaging integrity and operational efficiency.
Before implementing vacuum decay, the company faced challenges with high failure rates in incubation testing, leading to unnecessary product waste and costly inefficiencies. The bubble testing method lacked the sensitivity to detect micro leaks, allowing defective packaging to pass through quality control undetected. This resulted in undetected leaks compromising product safety, leading to costly recalls and damage to consumer trust.
Following the shift to vacuum decay testing with Oxipack’s flexible membrane technology, the company achieved a 60% reduction in incubation test failures. This improvement directly impacted quality assurance processes, enabling earlier detection of faulty packaging and reducing waste. Unlike destructive bubble leak testing, vacuum decay allowed the company to test without damaging packaging, making leak detection both sustainable and cost-effective.
Beyond improving accuracy and sustainability, the transition also enhanced regulatory compliance. Vacuum decay testing aligns with ASTM F2338 and USP <1207>, both of which are recognised by global regulatory bodies as the gold standard for deterministic, non-destructive leak detection. This shift positioned the company at the forefront of industry best practices, reinforcing its commitment to quality, efficiency, and consumer safety.
This example highlights how manufacturers can future-proof their operations by embracing advanced, non-destructive testing methods. By eliminating the limitations of bubble leak testing, businesses can reduce waste, improve detection accuracy, and ensure compliance with evolving industry regulations.
Meeting ISO and DIN standards
While ASTM F2338 already validates vacuum decay as a preferred leak detection method, upcoming DIN standard revisions are expected to formally incorporate it as a recognised approach for package integrity testing. These updates will further align global packaging standards with the shift toward non-destructive, deterministic testing.
Additionally, ISO 11607, which governs sterile barrier packaging for medical devices, aligns with the principles of vacuum decay testing by emphasising the need for validated, repeatable, and quantitative integrity testing methods. As regulatory bodies evolve their requirements, manufacturers adopting vacuum decay testing will be better positioned to meet current and future compliance standards while improving overall packaging reliability.
A leak-free future
Beyond regulatory compliance and improved accuracy, vacuum decay testing also supports sustainability goals. By eliminating the need to destroy tested packages, manufacturers can reduce material waste, lower costs, and improve environmental impact. In a time when corporate responsibility and sustainability are key concerns, adopting non-destructive testing is a strategic move for forward-thinking companies.
With proven success in major industries and growing regulatory recognition, vacuum decay testing is rapidly replacing bubble leak testing as the gold standard for package integrity testing. As more manufacturers adopt this advanced method, the benefits in efficiency, accuracy, and sustainability will continue to drive industry-wide change.
Oxipack has been at the forefront of this transition, working with global partners to refine and implement vacuum decay solutions tailored to the specific needs of the food, pharmaceutical, and medical packaging industries.