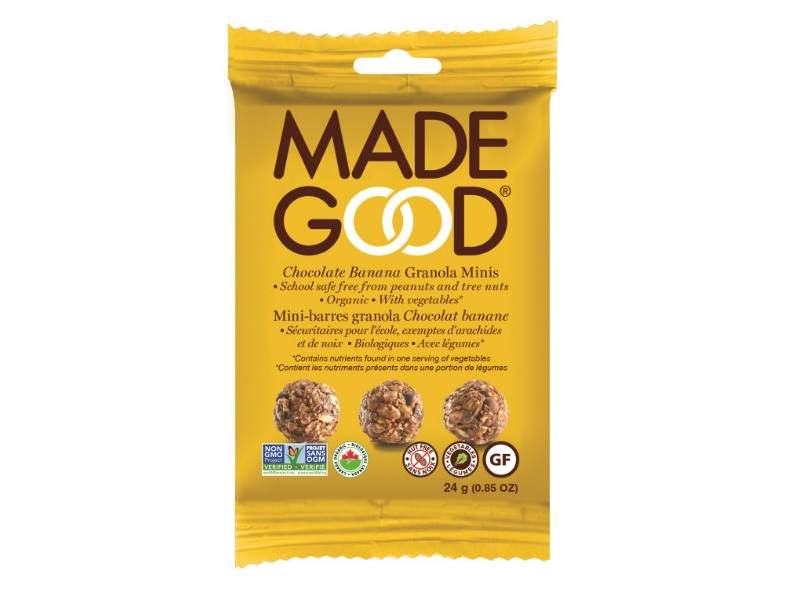
Riverside Natural Foods was able to double its packaging speeds by installing new packaging systems from tna.
Based in Vaughan, Canada, Riverside Natural Foods is a leading manufacturer of healthy snacks, such as organic snack bars and granola minis, under the MadeGood® brand. The company prides itself on the quality of its range of natural, allergen-free snacks and has seen a huge rise in the demand for its products since launching the brand back in 2013.
As a result of this immense growth, Riverside needed a partner that could deliver the high-performance packaging solutions and technical expertise to help them take their production volumes to the next level.
Healthy snacking on the rise
Growing health-consciousness amongst consumers has driven the demand for small bags of healthy treats to new heights. According to the latest consumer surveys, over 79% of global consumers confirmed that health and nutrition was important to them when choosing which product to snack on, making it the second most important factor after taste to influence their food choices.
“The way we snack has definitely changed over the past few years and so have consumer expectations on the product itself,” comments Sekhar Chakkingal, sales manager at tna. “A lot of consumers are leading extremely busy lives and are looking for healthy, on-the-go snacks that deliver everything: taste, convenience, and nutrition.
“This is good news for companies like Riverside which specialise in the manufacture of certified organic, highly nutritious snacks. Their range of Granola minis, for example, is ideal for consumers that need a quick nutrient boost that not only tastes great, but which is also able to fulfill their dietary needs.”
Meeting consumer demand
To help Riverside respond to the growing global demand for its 24g bags of granola minis, the company required a packaging system that could increase production volumes, simplify the company’s processes and reduce downtime. With previous packaging speeds ranging around 70-80 bags a minute, a high-speed bagging solution was at the top of the agenda for the snack manufacturer. At the same time, the system also needed to be hygienically designed and easy to clean to fulfill Riverside’s high sanitation standards and protect the allergen-free positioning of the company’s product portfolio.
High-speed packaging
The solution was the installation of two tna robag FX 3ci vertical form, fill and seal (VFFS) packaging systems. Renowned for its high speeds, the tna robag FX 3ci was able to offer both production flexibility and improved performance in a compact, easy-to-clean system. With its rotary double jaws, the new bagger was quickly able to deliver the company’s target speeds of 150 bags per minute, doubling the performance of the previous equipment and transforming Riverside’s production line efficiencies.
Integrated system solution
Featuring a small footprint to maximise the limited factory space available, the tna robag was delivered to Riverside as a completely integrated solution, which also incorporates tna’s intelli-weigh® 0314 omega series of high-speed multi-head scales.
Capable of up to 200 weighs per minute, the tna intelli-weigh 0314 omega offers high accuracy, reducing product losses and further improving the overall performance of the entire system. As a result, Riverside can now easily meet the demand of its rapidly growing customer base, while keeping waste to an absolute minimum.
Reliable date code accuracy
A clearly printed and accurate date code is vital to communicate the freshness of a product, meet regulatory requirements and avoid waste through rejected bags. Over the years, the bagging speeds of tna’s equipment have increased significantly to give manufacturers a competitive edge. However, operating at these high-speeds can result in extremely high and rapid changes of film speeds, which in turn can affect the ability of some date coders to print a clear code.
By opting for tna’s simple, yet highly effective film path adjustment system, Riverside is able to accurately adjust and control the film path position so that printing takes place at a point where the film’s velocity is within the date coder’s printing capability. As a result, Riverside is able to continuously achieve a clear and accurate date code print – even at 150 bags per minute.
Quality seal integrity
Riverside’s granola minis are packed with wholesome, certified organic ingredients, including a multitude of fine, particulate materials such as seeds, flakes and grains. To prevent fines from affecting the seal integrity of the bags, tna installed cross feeders with integrated sifter to remove small particles from the line before the product reaches the bag. In addition, tna’s product in seal detection (PISD) technology automatically triggers a reject mechanism if it detects product or particles in the seal area.
This means that Riverside is able to quickly remove bags from the line for further inspection before they enter the secondary packaging process. That way, Riverside is able to ensure that every bag meets the company’s high-quality standards, while keeping waste to an absolute minimum and reducing downtime for a more continuous production process.
Customer service culture
Commenting on the installation, Justin Fluit, VP of operations at Riverside says: “After reviewing all available options, we quickly realised that tna’s robag was the best solution for us to maximise our production capacities in the space available. No other vendor could deliver the speeds and offer options that also simplify operation and reduce downtime.
“The installation was smooth and we started hitting the target speeds shortly after setup. In fact, we were so impressed with the performance of the two systems that we immediately ordered a third bagger.”
Fluit adds: “The culture of the team at tna was also a big advantage. We visited the team at their Dallas office, where we were able to experience tna’s values and commitment to its customers first hand. All in all, it’s been an outstanding experience to see everyone from tna jump in to ensure we were satisfied and everything was working to specification.”