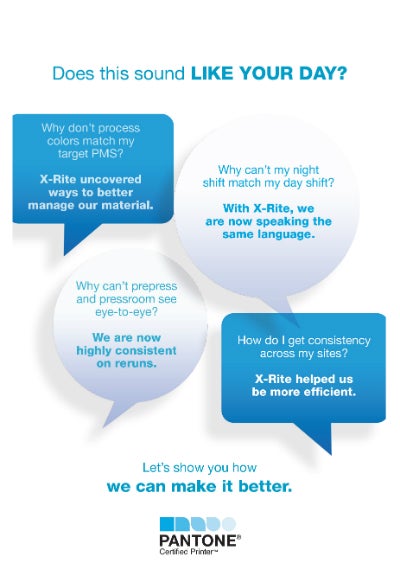
X-Rite Incorporated has announced the newly updated PANTONE Certified Printer Programme for commercial printers and packaging converters that addresses new industry standards.
The PANTONE Certified Printer Programme reviews and analyses every aspect of colour operations, from preflight, file preparation and proofing, to ink formulation and mixing, and process control in the pressroom. This creates total quality management based on industry best practices and procedures that drive consistent and repeatable colour.
"As a trade printer, you must be lean to be competitive," says Michael Clark, president of Cedar Graphics, an EarthColor company and a PANTONE Certified Printer. "The more I learned about the PANTONE Certified Printer Programme and how it could help streamline our processes and make them more consistent, the more interested I became."
he outside perspective that X-Rite Pantone brings to the PANTONE Certified Printer Programme enabled Cedar Graphics to ensure consistent operation from department to department and shift to shift, from ink room through prepress and the pressroom. "Everyone is now speaking the same language, and we are much more efficient as a result," Clark says.
The process begins with a PANTONE Certified Printer Audit conducted by an X-Rite specialist. The audit process isolates issues that compromise colour accuracy and is the basis for the implementation of Standards-Based Procedures so that all operators on all shifts can consistently produce the best colour the same way.
"The PANTONE Certified Printer Programme closes the gap that exists between the many other certification programmes available today which cover only part of the workflow, or simply a press or a proofer," explains Mark Gundlach, training development manager at X-Rite.
"This programme is unique in that it ties all areas of production together, from prepress and ink formulation to the press room with a focus on both process colour and spot colour reproduction. This applies to digital, flexo, litho and even grand format print production. Good printers can produce
great colour at a point in time but it may not be consistent over time. This programme, which includes a quarterly colour check based on a standard set of files, results in more consistent quality with less rework using existing investments and people."
"If you know you are going to be checked by an expert on a quarterly basis," Cedar Graphics’ Clark adds. "It’s just another incentive to keep things up to date as opposed to doing it once and forgetting about it. We look forward to our quarterly reviews and what we might learn each time that will help us communicate even better."
"Industry Standard Operating Procedures reduce variability across shifts and over time, as well as provide faster, more consistent staff training," Gundlach says. "Surprises cost money, and consistency reduces waste."
Proofing and printing to standards helps print and converting operations set and meet customer expectations. PANTONE Certified Printers follow standard operating procedures throughout the production operation when specifying CMYK colours based on their print standards. PANTONE colours are specified and formulated using spectral data from the PantoneLIVE™ digital libraries.
Packaging converters and printers interested in pursuing this certification to bring additional colour consistency, quality and efficiency to their operations not only benefit from the certification process but are also able to use the PANTONE Certified Printer logo to add even more credibility to their sales and marketing efforts.