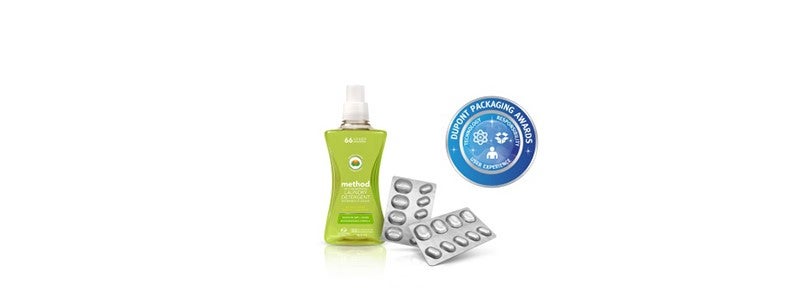
Amcor has won two gongs at the recent DuPont Packaging Awards with its pharmaceutical blister packaging and 100% post-consumer recycled PET bottle.
Amcor Limited, a global leader in responsible packaging solutions, has been recognized by the 28th annual DuPont Awards for Packaging Innovation competition for its leadership in delivering technologically advanced and sustainable solutions for the home care and pharmaceutical industries.
Amcor Rigid Plastics earned a Diamond award in the Technological Advancement, Responsible Packaging, and Enhanced User Experience categories for the development of a 53oz polyethylene terephthalate (PET) bottle for Method Products which contains 100% post-consumer recycled (PCR) PET resin. Meanwhile, Amcor Flexibles captured a Gold award in the Technological Advancement and Responsible Packaging categories for Formpack® Ultra, a new cold form blister packaging for the pharmaceutical industry.
The awards program is an international, independently-judged competition that honors innovations in packaging design, materials, technology, and processes across the entire packaging value chain. Inaugurated in 1986, the DuPont Awards for Packaging Innovation is recognized globally as the leading packaging awards program.
Amcor Partners with Method Products on First 100% Post-Consumer Recycled (PCR) PET Bottle for Liquid Laundry
"We are delighted to be recognized by DuPont for our commitment to innovation and sustainability," said Jim Rooney, vice president of sales for Amcor Rigid Plastics’ Diversified Products business unit.
"Our primary objective is partnering with customers and creating unique solutions like this 100% PCR PET bottle which delivers major sustainability benefits for Method and reinforces its strong environmental platform."
The 53oz sleek, transparent custom container, which delivers strong shelf appeal, is the industry’s first liquid laundry bottle made of 100% PCR PET. Well-known for its brightly colored hand wash and all-purpose cleaning formulations showcased in clear PET bottles, Method has broken new ground in the liquid laundry detergent aisle. In a market that has previously been predominately limited to high-density polyethylene (HDPE) containers, PET has struggled to enter the liquid laundry detergent market due to compatibility and color stability issues. Initially, Amcor provided product compatibility testing with Method’s liquid formula product to ensure package stability on the store shelf.
Amcor also worked through challenges with the container’s neck design, spout closure, and hand grips, ultimately creating a unique and sustainable design that could be stretch blow molded with a consumer-appealing hand grip.
The ergonomic design allows easy gripping and pouring and comfortable lifting. The new 100% PCR PET container meets high standards for sustainability with the package’s life cycle energy consumption reduced by 78% and its carbon footprint lowered by 35% versus a virgin PET alternative.
Amcor Rigid Plastics has a 24/7 on-site manufacturing facility at Method’s Chicago plant to help reduce transportation costs and lower Method’s carbon footprint. Amcor is making 100% post-consumer recycled PET bottles for hand wash and household cleaners at Method’s Chicago plant with production aided by wind energy. This is a first for an Amcor facility, which has reduced the need for 600 trucks of bottle freight and eliminated 200 metric tons of carbon dioxide emissions.
Amcor Flexibles’ Formpack® Ultra Delivers More Sustainable and Efficient Blister Packs
"We are thrilled to be recognized again with a DuPont Innovation Award," said Andrea Della Torre, R&D director for Amcor Flexibles. "Formpack® Ultra is a technical advancement and supports more responsible and sustainable packaging use across the value chain, while lowering the total cost of goods for pharmaceutical companies." This is the second award this year for Formpack® Ultra, which received an Alufoil Trophy in the Resource Efficiency category from the European Aluminum Foil Association in April.
Formpack® Ultra is a cold form blister product that offers greater elongation than standard cold form solutions, resulting in cavities than can be drawn deeper and with sharper wall angles than previously achieved. This achievement enables pharmaceutical companies to design smaller blister cards or add more cavities without increasing the blister card size. Formpack® Ultra’s superior elongation is possible thanks to "best-in-class" selection of raw materials, advanced manufacturing processes, and extensive quality control.
The smaller cavities enable better product protection as well as extended product shelf life and stability. In addition, the more efficient material usage of Formpack® Ultra provides the benefits of reduced changeovers at the customer’s site, together with the lower associated setup waste. hese factors result in a lower carbon footprint which decreases the total cost of goods.
Secondary carton packaging can also be diminished due to reduction in blister card size. Smaller blister cards also give companies the option to fit more blister packs into each carton box which contributes to optimized storage as well as fewer pallets and transport trucks.
Smaller blister packaging also offers better portability, making it more convenient for a patient to bring an individual dose in a single blister card to work or social events.