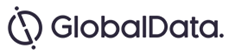
Last year, the global trade landscape faced significant hurdles, disrupting the supply chain and escalating operational costs. Labor disputes, such as the United States port strike in October, brought operations to a standstill at 36 ports along the East and Gulf Coasts, resulting in shipment delays and increased expenses. Geopolitical tensions in the Red Sea further complicated maritime trade routes, leading to additional shipping delays and a rise in insurance premiums. Moreover, extreme weather events, including droughts affecting the Panama Canal, restricted vessel transit and disrupted the flow of goods worldwide.
Modern supply chains are also extremely complex, spanning thousands of suppliers and various moving parts across oceans and continents. While this can help mitigate the impact when one supplier encounters delays, it still presents mounting logistical challenges. The materials may now be coming from or located in a completely different area, requiring a new plan to get them to their required destination.
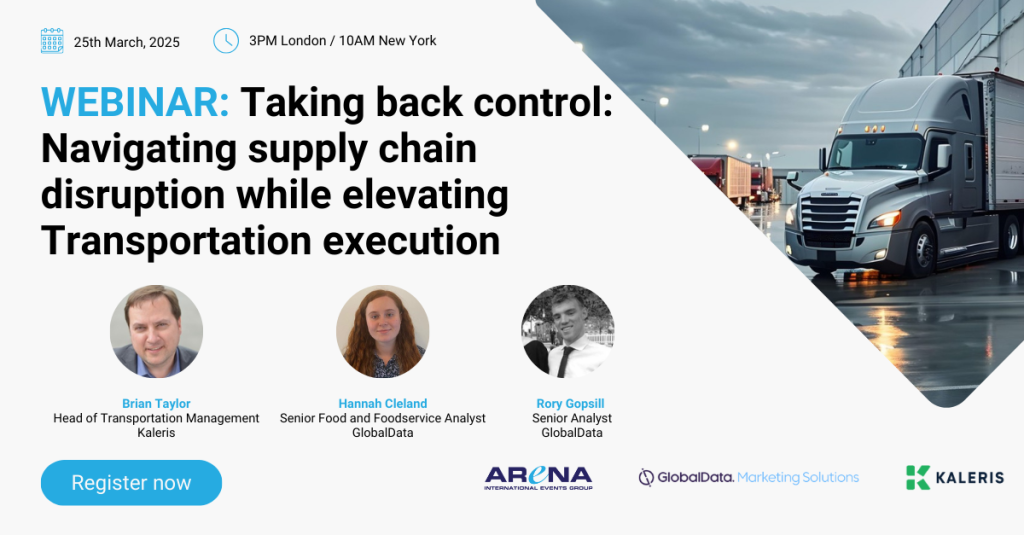
Such challenges lead to market variability and unpredictable goods availability, which has a huge knock-on effect on a business’s overall efficiency and expenses. Faced with challenges of this scale, businesses might feel that easing supply chain difficulties is beyond their control. However, actions can be taken to address operational efficiencies much closer to home.
The yard: an overlooked area for investment
The yard is historically overlooked as an area worthy of improvement, with management often caught between the transportation and warehousing departments. As a result, many yards continue to be managed with traditional pen, paper, and radio methods.
“The conflict between transportation and warehousing causes indecision,” says Eric Breen, director of enterprise sales at Kaleris, a global leader in yard management solutions. “As a result, opportunities are lost.”
A YMS is a vital tool for improving efficiency and reducing costs across supply chains, with significant macroeconomic implications. By streamlining yard operations at distribution centers, warehouses, and terminals, a YMS eliminates bottlenecks and reduces truck dwell times. This optimization directly lowers transportation costs, improves resource utilization, and boosts productivity across industries. These cost efficiencies can cascade through the economy, enabling businesses to offer competitive pricing, manage rising logistics costs, and maintain supply chain continuity during disruptions.
With yards frequently experiencing high staff turnover, the weaknesses of these outdated systems are too often exposed. Without a central source of information, yard managers will struggle to run an effective operation, thus contributing to further delays and expenses.
“There’s a lack of knowledge on how a well-run yard can contribute to overall cost reduction and efficiency improvements,” adds Breen.
The benefits of combined yard and transport management
Investing in a digital yard management solution (YMS) presents significant opportunities for optimizing supply chain operations over traditional pen-and-paper methods. Reducing labor requirements and margins for error, the right YMS can also improve the visibility and accuracy of data to improve asset utilization.
Industry leaders Kaleris have developed a holistic digital yard management solution that can manage the demands of even the most complicated supply chains. Through the Kaleris YMS, employees can build a personalized dashboard to support their work. Users can see time and cost reductions in a variety of manual processes, from checking in gate staff to carrier performance tracking, and overall improvements can be seen in the visibility of asset inventory, documenting drivers, and yard activity metrics.
“You shouldn’t have to actively manage a yard if you have the workflows built into the YMS like ours is very capable of doing,” says Breen.
Combined with a digital transportation management solution (TMS), the YMS becomes an extremely powerful tool. Together, the digital systems organize the speedy movement of trucks and trailers, including the scheduling of inbound and outbound trucks to reduce bottlenecks at docks.
Kaleris’ trusted partners include grocery chains such as Albertsons and Kroger, whose complex supply chains require the management of fresh produce. Kaleris’ YMS and TMS work together to streamline cold chain logistics, from the provision of data analytics to identifying patterns in peak times to refine logistics strategies and improve delivery reliability. This ultimately improves on-shelf availability goals and produces a better overall service for shoppers.
Optimizing logistics management
As a partner in logistics management, Kaleris stands out for its end-to-end solution that can address critical pain points within the supply chain. The integration of TMS and YMS eliminates communication gaps and handoff delays, reducing those bottlenecks that can be critical to the successful delivery of perishable or high-demand goods.
Functioning on a single platform, all stakeholders across logistics have access to the same data in real-time, thereby enabling more proactive decision-making. Making a conscious choice to coordinate yard, transport, and warehouse activities in this manner translates to significant savings in labor and asset management.
“The product has been pulled in lots of different directions based on many different customers across different verticals, so we’ve been able to accommodate so much,” notes Derek Pedersen, senior technical product manager at Kaleris. “There’s very little stock configuration. Customers can build their own yard management solution, on a yard-by-yard basis.
“It’s about giving you what you need to run an effective, compliant, and operational facility. Our solution lets managers draw the lines and color the page according to their requirements.”
With supply chains today facing so many unprecedented challenges, Kaleris’ digital solutions equip companies with the tools they need to maintain efficiency and minimize the impact of disruption. To learn more, download the free whitepaper below.